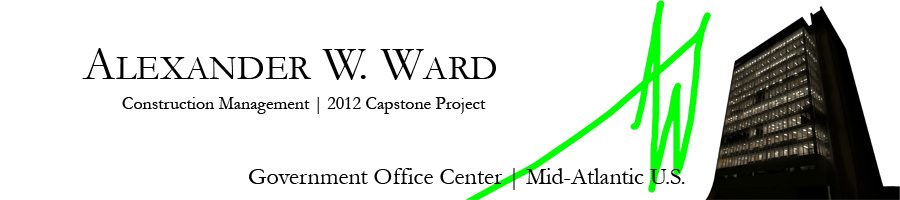
|
 |
|
|
Building Statistics |
|
Part I |
|
|
|
General Building Data |
Building Name
Location
Building Occupant
Occupancy Type
Size
Total Levels
Dates of Construction
Overall Project Cost
Project Delivery Method |
|
Government Office Center
Mid-Atlantic United States
U.S. Federal Government
B - Offices and Courts
316,000 SF
14 Floors above grade
August 2011 - February 2014
$42.5M
Design-Build |
|
|
|
Primary Project Team |
U.S. General Services Administration
Balfour Beatty Construction
TranSystems Corporation
Thornton Tomasetti
Greenman - Pedersen, Inc.
William McDonough + Partners
GAI Consultants, Inc. |
|
Owner
CM
Architect
Structural Engineer
MEP Engineer
Sustainability / Design Consultants
Civil / Landscaping |
|
|
|
Architecture |
+Design and Functional Components:
Originally designed and constructed in the mid-1970s, this modernist high-rise is essentially a rectangular building with sides facing nearly North, South, East, and West. The East and West facades are a uniform tan brick from top to bottom, without any breaks for windows. The North and South facades are large glass curtain walls spanning almost the entire building height, allowing relatively uniform diffuse daylight to enter the building from the North while more intense and direct sunlight enters the building from the South.
The first three floors contain courtrooms and rooms that serve functions relating to courtroom activities. The remainder of the building contains the offices, file storage, IT spaces, and other functions needed to serve an office building of this size.
+Major National Model Codes:
International Building Code (IBC) 2006 edition
International Fire Code
+Zoning:
The project is located within a downtown multipurpose zoning district, which allows it to have no building height or footprint restrictions. However, there is a maximum floor area ratio (FAR) of 15.0.
+Historical Requirements:
No historical requirements known at this time, although the project will be maintaining the familiar appearance of the existing building.
|
|
Building Enclosure |
+Building Facades:
The East and West facades consist of a uniform and continuous tan brick from the top of the building to the bottom, while the North and South facades are large glass curtain walls (as shown in Figure 1) spanning almost the entire building height. The replacement of the existing curtain walls with an improved unitized curtain wall system constitutes a significant portion of the project costs.
+Roofing:
New roofing installation will include SBS modified bituminous membrane roofing in some areas of the roof and EPDM membrane roofing in other areas. Roofing systems will use foam-plastic board insulation and lightweight insulating concrete. For example, in one area of the roof, there will be three layers of 3-inch thick polyisocyanurate and a half-inch thickness of DensDeck Prime.
|
|
Sustainability Features |
This renovation project will incorporate improvements to the building’s HVAC systems, water efficiency, and lighting, which ultimately will reduce the energy demands and carbon footprint of the building.
In order to reduce unwanted direct sunlight from entering the building, motorized roller shades, a passive sustainability feature that reduces thermal gains while improving interior lighting conditions by helping to eliminate glare and excessive contrast, will be incorporated into this project.
An active sustainability feature of this project is a ballasted photovoltaic panel array that will support a portion of the building’s electricity demand, thereby reducing its dependence on utilities and adding a level of stability to its energy costs.
|
|
|
Part II |
|
|
|
Project Delivery System |
The Government Office Center renovation and modernization project is being delivered under a Design-Build system with an Advisor to the Owner and a Construction Management Contractor. Balfour Beatty Construction was selected for preconstruction services with the option for GSA to extend the scope of the project to include the renovation work itself. After this option was activated, Balfour Beatty Construction began awarding lump sum contracts to a variety of subcontractors to handle the scope of work involved in the Government Office Center renovation project. Perhaps most significant among these subcontracts, based on scope of work, are the curtain wall contract, mechanical and electrical contract, and demolition contract.
The Guaranteed Maximum Price contract is appropriate for the construction management team because of its involvement in the preconstruction phase of this project, giving Balfour Beatty Construction a fair opportunity for reward while holding them accountable to some degree for proper performance of the renovation work. Lump sum contracts are logical for subcontracts and for design and consulting efforts on a renovation project like this. The cost-plus-fee contract with the Advisor to the Owner is also appropriate, since the cost of work is limited already by the GMP with the Construction Management Contractor.
Payment and performance bonds are required for this project, as well as Owner’s insurance to protect the Owner and project team from liability for major damages to the Owner’s property during the demolition and renovation work.
|
|
Site Layout Planning |
This renovation project is being performed on a fairly constrained site. Using parts of the existing parking areas on site, the construction management team will place trailers, temporary air handlers, and material laydown and storage areas according to the needs of the project. The space is limited to the extent that there is no on-site parking available to the construction management team or the subcontractors.
|
|
Demolition |
Demolition makes up a critical portion of the renovation of the Government Office Center. However, due to the ongoing occupation of the building during the demolition activities, as well as the salvage and recycling goals of the owner, there are specific instructions for how to handle many aspects of the demolition. For example, demolition of existing built-up roofing must be performed outside normal working hours. Also, particulate discharge resulting from demolition, cutting, grinding, and sandblasting operations must be controlled, and water sprinkling must be used, where relevant, as a means to control dust generation.
Before beginning demolition work, photographs must be taken of the existing conditions, including each window wall interior and exterior, each roof including existing items to remain during construction, and mechanical rooms from a variety of different vantage points.
The project specifications call for very specific descriptions regarding the conditions that must be met for a variety of materials being removed from their existing locations as part of the demolition process. These specific guidelines illustrate one of the goals of the owner for this project, which is to salvage and recycle as much non-hazardous demolition waste as possible. Concrete demolition requires the removal of reinforcement and other metals from the concrete and pulverization of the concrete to a maximum 1½ inch size, while masonry must be pulverized to a maximum ¾ inch size. Wood materials and structural steel to be recycled must be sorted and stacked according to size, type, and length. Large, clean pieces of gypsum board and acoustical ceiling panels and tile must be stacked and stored in a dry location. Large pieces of carpet and pad must be tightly rolled and stored in a closed container. Equipment, tanks, and fixtures must be drained, have their openings sealed, and be protected from exposure to weather. Piping and conduit must be reduced to straight lengths and stored by type and size. Lamps should be separated by type and protected from breakage.
The extensive existing aluminum and glass curtain wall system must be demolished, along with partitions and finishes within the perimeter zone of the building adjacent to the curtain wall. Also, certain existing HVAC systems within the building will be removed and replaced as part of the scope of work of this project. The existing systems to be removed include a cooling tower and chillers, boilers, air handling units, and perimeter electric baseboard heating system.
Asbestos is known to be on this project site, and will affect the demolition work to be performed. All work involving the contact, disturbance, dismantling, and/or disposal of hazardous materials must comply with the applicable requirements of 29 CFR 1926/1910 and 40 CFR 761, particularly (in the case of asbestos) 40 CFR, Part 61, Subparts A and M. Work must also comply with applicable state and municipal safety and health requirements. Specifically, existing built-up roofing systems, including membranes, felts, asphalt, tar, sealant, or adhesive on the roof and flashing system contain asbestos. Therefore, during the demolition of the existing lower and upper roof areas, all roofing materials and components are to be handled as Asbestos Containing Roofing Material (ACRM).
|
|
Structural Steel |
The existing structural steel frame supports the building, with a middle bay of open space spanning from the East to West sides of the Government Office Center. This middle bay is flanked on either side with narrower bays of equal width which connect to the curtain wall frame. Floor loads are handled by one-way slab-on-deck before being transferred to trusses. Existing W-Shape steel columns transfer loads vertically into the foundations of the building.
New Hollow Structural Section steel members will be installed on the North and South facades to support the load of the new curtain wall, ranging in size from HSS6x6x1/2 on the third floor to HSS8x8x3/8 on the thirteenth floor. No crane will be used on site, instead this need will be handled by the use of davits.
|
|
Cast-in-Place Concrete |
Cast-in-place concrete exists on this site in the form of foundations and slab-on-deck flooring. This renovation project will require the addition of a new level slab for a new revolving door on the foundation level, as well as filling in gaps where it was necessary to chip away existing concrete.
|
|
Masonry |
Existing concrete masonry unit walls in the South area of Level 2 will be rebuilt with greater reinforcement to act as part of the lateral load resisting system. Large existing expanses of masonry on the East and West facades will not be involved in the scope of the renovation of the Government Office Center.
|
|
Mechanical System |
Mechanical rooms are located on the 1st and 14th floors. Air handling units present in the Government Office Center will be replaced and improved through the addition of variable flow valves. Existing perimeter electric baseboard heating will be replaced with VAV boxes with hot-water reheat that will distribute to new perimeter slot diffusers. The existing cooling tower and chillers will be replaced by two 300-ton centrifugal chillers, and the system will be converted to variable primary flow. Also, existing boilers will be replaced with more energy-efficient natural gas-fired boilers.
All ductwork existing in the Government Office Center that is not removed and replaced is scheduled to be cleaned as part of the scope of this renovation project. Sub-metering will be installed to help the building facilities management team to monitor and control energy use within the Government Office Center. The air filtration system will also be upgraded as part of the renovation and modernization of this building.
|
|
Electrical System |
The Government Office Center is currently powered by an existing 480/277, 3 phase, 4 wire system that is backed up by a 175 kW, 219 kVA emergency generator. As part of this project, some electrical panels will be replaced to handle the renovated lighting system. Other new electrical work includes the necessary connections for two new chillers, each of which has a compressor drawing 183kW from a 460V, 3 phase connection.
|
|
Lighting |
A significant portion of the lighting scope of work on this project involves the demolition and replacement of existing luminaires in favor of more energy-efficient fluorescent, compact fluorescent, and LED fixtures. For example, T-12 fixtures will be replaced throughout the building, and LED lighting will be added as part of the toilet room renovations. Energy efficient lighting and controls will be installed throughout the Government Office Center. Part of this effort includes daylight harvesting and occupancy sensors to help reduce electricity demand.
|
|
Curtain Wall |
The existing curtain wall on the North and South facades will be replaced with a unitized, aluminum-framed curtain wall assembly. The intent of this portion of the renovation is to offer drastic improvement to the thermal performance of the building envelope, which in turn reduces the demand on the mechanical systems of the Government Office Center. Structural properties for this curtain wall system include the ability to withstand a basic wind speed of 90 miles per hour, while thermal movements should not cause undue stress on any building element that connects to or is part of the curtain wall system. The system is designed such that water drains to the exterior face of the curtain wall without any harm to neighboring surfaces or insulation.
During this project, a temporary engineered weather wall will separate the work zone from the occupied building areas. The existing system will then be removed on a specific floor, working from top to bottom. A material hoist on the Northwest corner of the building will allow for the transfer of materials and large waste products into and out of the building.
A single firm is required by the project specifications to assume undivided responsibility for fabrication, installation, and coordination of all elements of the building enclosure renovation. Responsibility for the design is in the hands of a design entity with extensive international experience in engineering, project management, fabrication, and installation of curtain wall systems.
|
|
LEED Certification Goals |
The Government Office Center renovation and modernization project must achieve a minimum LEED Silver Certification. The cost of the initial application is carried by the A/E, while all other costs are the responsibility of the CM. Recycling and salvage of demolition waste as well as recycling of construction waste is an important part of this effort. Since the renovation of the curtain wall and mechanical systems will greatly improve the energy performance of the Government Office Center, several LEED points will also be earned from the Energy and Atmosphere credits.
|
|
Fire Protection |
Existing fire sprinklers within the workspaces surrounding the curtain wall will be partially demolished and adjusted to serve as fire protection between the weather wall and building exterior during the construction phase. Substantial sections of existing fire protection systems will be demolished and replaced with new, NFPA 13 compliant sprinkler coverage that is fully coordinated with the new ceiling layout.
|
|
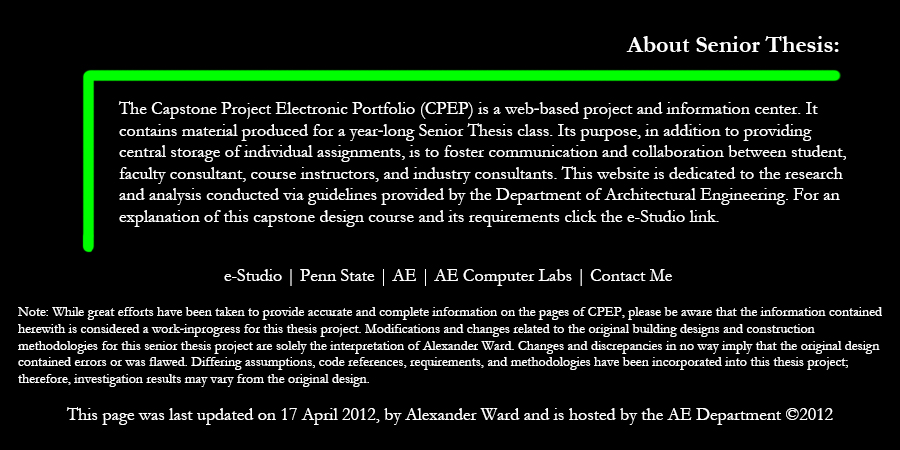
|