Home
Student Biography
Building Statistics
Thesis Abstract
Technical Assignments
Thesis Research
Thesis Proposal
Presentation
Final Report
Reflection
Senior Thesis e-Studio
|
Project Team: |
Building Statistics |
Building Name |
Butler Health System – New Inpatient Tower |
Location |
Butler, PA |
Occupant Name |
Butler Health Care Providers |
Function |
Surgery and Recovery |
Size |
New construction – 206,026 square feet |
Renovations – 16,555 square feet |
Total Height |
134 feet – 3 inches |
Number of Stories |
Above grade – 6, Below grade – 2 |
Use Group |
1-2 Hospital (Non-separated mixed use) |
Construction Type |
1B (NFPA Type2 (222)) |
(Reduction per IBC 403.3.1) |
Construction Dates |
Start – September 2008 |
Projected finish – July 2010 (expected) |
Delivery Method & Cost |
GMP (Guaranteed Maximum Price), $93M |
|
Owner: Butler Healthcare Providers |
www.butlerhealthsystem.org |
Owners Representative: Ritter Construction Management Inc. |
www.ritterpm.com |
Construction Manager: Turner Construction |
www.turnerconstruction.com |
Architect: Design Group |
www.dgcolumbus.com |
Design Architect: Hammel, Green, Abrahamson |
www.hga.com |
Civil & Environmental Engineering: Pedersen & Pedersen |
www.pedersenx2.com |
Technology Engineer: KJWW |
www.kjww.com |
Equipment Planner: Korbel Associates |
www.korbel.net |
Elevator Consultant: VDA Associates |
www.vadssoc.com |
|
Note: While great efforts have been taken to provide accurate and complete information on the pages of CPEP, please be aware that the information contained herewith is considered a work‐in‐progress for this thesis project. Modifications and changes related to the original building designs and construction methodologies for this senior thesis project are solely the interpretation of Jim Rotunno. Changes and discrepancies in no way imply that the original design contained errors or was flawed. Differing assumptions, code references, requirements, and methodologies have been incorporated into this thesis project; therefore, investigation results may vary from the original design. |
Sustainability Concepts:
The design of the large glass atrium area extending up two levels from the second floor in the main reception and waiting areas provides natural daylighting that extends deep into that level.
White EDPM roofing membrane helps with reducing the solar gain from the roof system.
Low E and high performance glazing provide heat gain/loss resistance.
Room occupancy sensors and double switching for multiple lamp fixtures will reduce light energy consumption. |
Architectural Features:
The architectural form of the building on the North side reflects the contour of the topography with the stepped walking path, and the curvature of the roadway with respect to the arcing wall of the North facade. Each level of the new addition has specific functions with the Ground and first floor levels being devoted to emergency generators, elevator pits, mechanical, electrical, boiler, chiller and storage rooms as well as some staff support areas. One quarter of the second floor area is given to training rooms, while approximately another quarter is seating / waiting areas; and the balance is given to an auditorium, chapel, physician lounges, a boardroom and conference rooms. Third floor space is devoted to the Ambulatory Care Unit, operating rooms and outpatient surgery. Fifth floor space is the Critical Care Unit and its support facilities. Floors six and seven are patient recovery rooms. On the top level of the structure is the penthouse level which houses the air handling units and mechanicals. 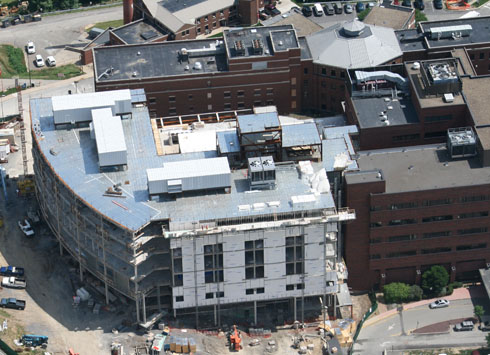 |
Building Enclosures:
Wall systems are primarily composed of a brick veneer with an air space on two inch polisocyanurate rigid insulation attached to 6”structural metal studs sheathed on both sides with 5/8” gypsum wall board and filled with 6” batt insulation. Glazing systems for the exterior walls are a glazed aluminum curtain wall system manufactured by Wausau and utilizing the Wausau “2-1/2 Inch Face Superwall/Pressure Wall Series”. Sealed insulating glass units are primarily 1” tinted insulating glass: ¼” tinted exterior light equal to PPG Gray with a low “E” coating matching Viracon VE3-2M on surface #2, 1/2 inch air space, ¼ inch clear interior light. Heat strengthened both lights.
Roofing is an insulated membrane assembly with Carlisle “Sure-Weld” thermoplastic polyolefin (TPO) membrane formed into uniform flexible sheets with a nominal 60 mil thickness and mechanically secured as per manufacturers installation instructions. |
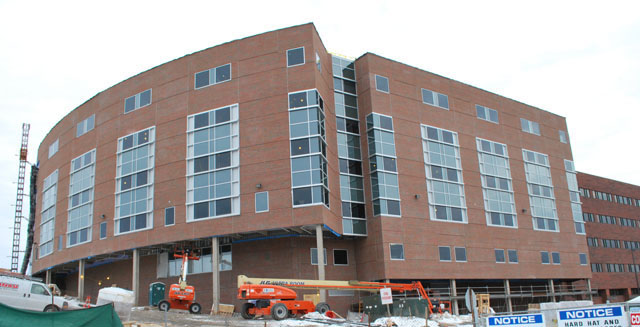 |
Applicable Building Codes:
This building is designed to comply with:
The 2000 NFPA 101
The 2006 International Building Code
The 2006 Guidelines for Design and Construction of Health Care Facilities
The 1998 Pennsylvania Department of Health Rules and Regulations for Hospitals |
Zoning:
City of Butler Zoning Regulations
1-2 Hospital ( Non-separated mixed use)
1B (NFPA Type 2 (222))
No Building Floor Height Limitations
|
|
|
Mechanical Systems:
Heating, ventilation and air conditioning (HVAC) requirements are being provided through the use of eight air handeling units (AHU's) at the roof top levels. AHUs 1,2&3 supply 62,000CFM each of conditioned air, while AHUs 4&5 supply 18,500, AHU 7 supplies 4000 and AHU 6&8 supply 4700CFM each.
The HVAC system consists of 3 chillers, two 400ton and one 119ton, which supply the cool water for AC while two 7200MBH water tube boilers supply the hot water for the heat to the AHUs. From the AHUs conditioned air is forced through the building to individual variable air volume (VAV) boxes closer to the discharge destination which which readjusts the airs quality again before delivering it to individual rooms.
Bare fin tube radiant heat is utilized in the soffit areas under the floors on first and second levels.
Radiant ceiling panels are used on the fifth, sixth and seventh floors along the perimeter walls in conjunction with the forced air system. |
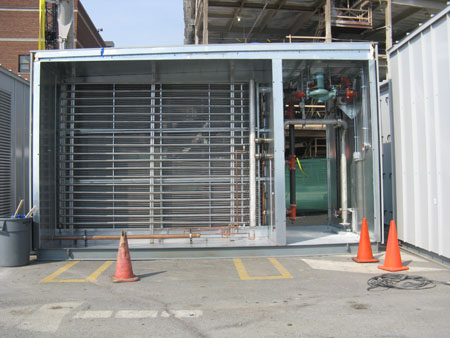 |
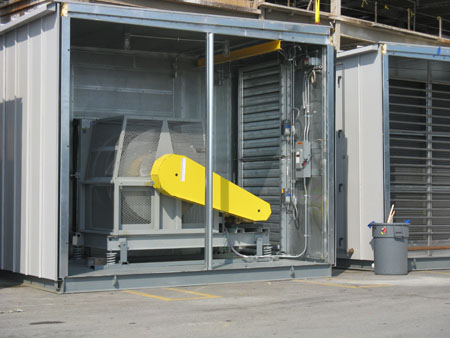
|
Fire Protection Systems:
Spray-on fireproofing has been applied to all structural columns beams and load carrying HSS bracing members.
The addition is required to have a fully spinkled system installed including a standpipe for fire department hook up.
A combination of fire and smoke rated walls, floors, ceilings,partions and barriers are located throughout and range from 1-3 hours. |
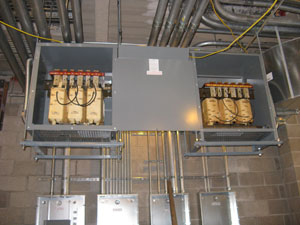 |
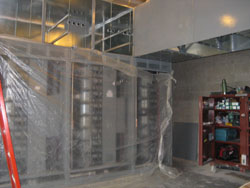 |
Special Systems:
A pneumatic tube delivery system is used throughout the building to transport various items such as documents, medications or other light materials.The system is designed by Swisslog and is designed to meet the unique transport requirements of hospitals fast, accurate reliable and securely.
BIM modeling is being used on the project as an ongoing basis to accurately and quickly identify system clashes before they are implimented. To date it has been a success as some systems had not been fully designed before construction started, such as medical equipment supports and bracing.
|
Electrical:
The power supply enters the structure from the existing building into the first level electrical room on the plan west side of the addition where it comes into the 2500kVA transformer which supplies power the building. The main and emergency electrical rooms have panelboards for both 208/120V and 480/277V 3 phase 4 wire feeds and panels. There is at least one electrical room located on every floor to supply both the high and low voltage needs for the lighting, equipement and general usage power requirements. Emergency backup power is supplied by a standby generator located on the ground level directly under the main electrical rooms.
Lighting:
Lighting requirements in a hospital setting vary widely and can be extremely critical in an operating and emergency room setting.
There are 85 different type of lighting fixtures located throughout the hospital to meet all of the unique and demanding needs for the varying settings and room requirements.
This system of varying fixtures also employes the need for varying lamp types including but not limited to incadescents, flourescents, and compact flourescents all of which are supplied by either 120V or 277V.
|
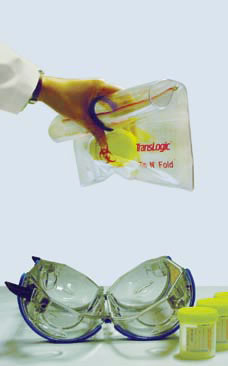 |
 |
Photos from Swisslog |
|
|