Note: While great efforts have been taken to provide accurate and complete information on the pages of CPEP, please be aware that the information contained herewith is considered a work‐in‐progress for this thesis project. Modifications and changes related to the original building designs and construction methodologies for this senior thesis project are solely the interpretation of Nicholas Ziegler. Changes and discrepancies in no way imply that the original design contained errors or was flawed. Differing assumptions, code references, requirements, and methodologies have been incorporated into this thesis project; therefore, investigation results may vary from the original design. |
|
Building Statistics
General Building Data
Building Name |
Belmont Executive Center; Building A |
Location and Site |
19755 Belmont Executive Plaza
Ashburn, VA 20147 |
Building Occupant Name |
Toll Brothers VA Division
Westminste Title
Melbourne IT
Variplan |
Occupation/Function Type |
B-Business, Multi-Tenant office space
|
Size |
124,661 SF |
Number of Stories Above Grade |
5 |
Primary Project Team |
Owner - Toll Brothers Commercial
General Contractor - L.F. Jennings
CM - General Contractor played the roll of the CM
Architects - The M Group Architects
Civl Enigneer - Eastern States Engineering Inc.
Structural Engineer - Haynes Whaley Associates Inc.
MEP Engineer - KTA Group, Inc.
Landscape Architect - Urgan Engineering & Associates
|
Dates of Construction |
9.21.06 - 7.19.07 |
Project Cost Information |
Information witheld at owner's request
|
Project Delivery Method |
Guaranteed Maximum Price (GMP) |
Architecture
Major National Model Codes |
Virginia USBC (2000 IBC)
IBC 2000
NFPA 12, 14, 24
1999 NEC |
Historical Requirements |
None |
Zoning |
Loudoun County Zoning Ordinance |
Architecture (Design and Functional Components)
The Belmont Executive Center serves as a multi-tenant office building. A large atrium space extends from the ground floor up to the first floor in the front entrance of the building. The ground floor is divided into three separate tenant spaces, and there is an elevator lobby, restrooms, and mechanical spaces located in the center of the building. All other floors offer flexible office space, and has the same central core as the ground floor. Each floor can be divided into the desired amount of tenant space. An exterior terrace is accessible from the fifth floor and overlooks the rear of the site.
Building Enclosre
Building Facades
The Belmont Executive Center is a masonry building, primarily built with face brick on lighted gage metal studs. On the front of the building are large EFCO System 5600 glass curtain walls. They are on both ends of the building and at the central entrance, and extend from the ground floor up to the roof. The central part of the building rises three feet above the parapet edge to distinguish it from the rest of the building. The rear of the building has the same EFCO System 5600 curtain wall in the center of the façade, but not on the ends. All other windows in the building are an EFCO System 400 storefront, and are divided by vertical columns. Arristcraft CMU blocks accent the face brick, and are used as lintels, provide a horizontal break between floors two/three and, and create a base for the vertical columns. The mechanical equipment is shielded behind a metal screen on top the building. 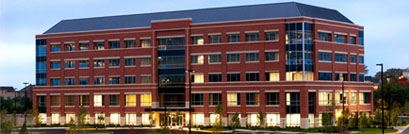
|
Roofing
The main roof is a typical built up roof composed of 1/2" denseglass deck, 1 1/2" coverboard insulation, and 1 1/2" thermal insulation. All the girders supporting the roof are angled at 1/4" per foot to produce the roof's slope. On the fifth floor balcony the roof is a modified bitumen hot rubberized asphalt roofing with rigid insulation and protection board. |
Sustainability Features
Leed certification was not part of the intial program. Energy saving features have been incorporated into the basic design such as a heat exchanger to provide "free cooling" and glazing with little thermal transfer. Water closets and urinals are equipped with motion sensor operated flush mechanisms.
Primariy Engineering Systems
Construction
Construction of the Belmont Executive Center; Building A began on September 9th 2006. All work was completed in less than one year, and the building was fully constructed by July 19th of the following year. The general contractor on the job was L.F. Jennings, and the company also scheduled and managed the construction process. A Guaranteed Maximum Price (GMP) was used as the project delivery method.
Electrical/Lighting
Electricity to the building is provided by a 277/480 volt, 3phase, 4 wire switchboard with a 4000 amp bus duct. A 600kW, 480V, 3 phase diesel generator with a 900A output circuit breaker was installed to provide emergency power if needed. There are individual transformers for each floor to step down the supplied voltage to 120-208V. Three are located on the first floor; one 75KVA 480/120-208V transformer in the main electrical room, and one 45KVA 480/120-208V transformer in both tel/elec rooms. Floors 2-5 have a total of two 75KVA 480/120-208V transformers, with one in both tel/elec rooms. Panels are located before and after entering the transformer, providing both 480V and 120-208V panels for each floor. Artificial lighting is produced by a combination of fluourescent strip, pendant, recessed, and sconce lighting fixtures.
Mechanical
There are two 14000 CFM self contained units per floor, with a variable control system supplying heating and colling to the north and south (left/right) zones of the building. Heat generated by occupants and office equipment provides most of the heat for each floor, but each self contained unit has an electric heating coil to provide additional heat. Individual wall heaters help supplement the heating load at both side entrances on the left and right side of the building. Cold and hot water is provided by individual water heaters/chillers per floor, and there is a 344 ton cooling tower with a heat exchanger located on the roof. The cooling tower removes heat from the cooling system and the heat exchanger takes advantage of cold outside temperatures to provide "free cooling".
Structural
The Belmont Executive Center; Building A is a steel frame construction building with large spans in the North-South direction to provide optimal office space. Steel columns are supported by square spread footings, and first floor is a 5" slab on grade. At the middle right side of the slab on grade, a small portion of the slab is increased to 6" to support a 30 yard trash compactor. Around the perimeter of the building, grade beams connect the spread footings, and support the masonry facade. The floor system is constructed of 3 1/4" of light weight cocnrete on 3" of 18 GA. metal deck. Composite action is achieved through shear studs welded to the beams.
Concentrically braced steel frames provide lateral support for the building. All the columns and beams in the system are fabricated from W Shape steel members and cross bracing is provided by square HSS steel. There are three braced frames located in the long direction of the building, and one located in the short direction of the building.
Most columns in Building A are W shape steel columns, but some are rectangular HSS steel members. The reason for the HSS steel members is the need to provide adequate support strength in locations where wide flange steel columns would not fit in the space requirements dictated by the architecture.
The roof of the building is supported by K series bar joists on both the main level and the penthouse level. Bar joists on the main roof level were designed specifically for snow drifting loads. Drifts were assumed to occur against the parapet and the penthouse wall. All joists located in an area where drifts could occur were specially designed by the joist manufacturer to carry the required loads.
Engineering Support Systems
Fire Protection
All beams located in the central core of the building are 2 hour fire rated, as well as all columns located in this area. On the second floor the beams and columns are also rated for 2 hours, along with the slab located in the core and the upper left and bottom right of the building. Floors 3-5 only have 2 hour rated slabs located in the middle bay of the building, and the beams and columns are identically rated to the ones below. An automatic sprinkler system is installed in accordance to NFPA 13, 14, 24 throughout the building, with a fire connection located at the left side of the main entrance. A 750 GPM@75 PSI, 75 HP, 480V, 3 phase fire pump supplies pressure to the risers and stand pipes located in the stairwells. To maintain the pressure a 8 GPM@125 PSI, 3/4 HP, 480V, 3 phase jockey pump was installed.
Transportation
In the center of the building there are three stairwells, one of which accesses the penthouse.The sairwells are enclosed by a 2 hour fire rated partition constructed of two layers of gypsum board on metal studs. The main mode of vertical circulation is acheived by three elevators located in the center of the building.
Telecommunication
Three 3" conduit sleeves per tel/elec room distribute the communication services vertically through the floors. There is one tel/elec room on the first floor, and two on the remaining floors. Each tel/elec room is located in the same location on each floor. |