|
User Note:
While great efforts have been taken to provide accurate and complete information on the pages of CPEP, please be aware that the information contained herewith is considered a work‐in‐progress for this thesis project. Modifications and changes related to the original building designs and construction methodologies for this senior thesis project are solely the interpretation of Adam Love. Changes and discrepancies in no way imply that the original design contained errors or was flawed. Differing assumptions, code references, requirements, and methodologies have been incorporated into this thesis project; therefore, investigation results may vary from the original design.
|
|
|
|
|
|
|
Building Statistics
General Building Data:
|
|
|
|
|
|
|
|
Building Name: |
|
Building 31 & 32 - FDA OC/ORA Office Building |
|
Location and Site: |
|
White Oak Federal Center, Silver Springs, Maryland |
|
Building Occupant: |
|
Food and Drug Administration |
|
Function: |
|
Office Building with Mixed Use of Assembly |
|
Size: |
|
500,000 S.F. |
|
Number of Stories: |
|
Building 31: 4 stories plus 1 below grade |
|
|
|
Building 32: 5 stories plus 1 below grade |
|
Dates of Construction: |
|
June 2007 to December 2009 |
|
Final Contract Cost: |
|
$110 Million |
|
Project Delivery Method: |
|
Lump Sum Project |
|
Project Team: |
|
|
|
|
Owner: |
|
|
|
Occupant |
|
|
|
General Contractor: |
|
|
|
Construction Manager: |
Heery-Tishman |
|
|
Architectural Engineer: |
|
|
|
|
|
|
|
Geotechnical Engineer: |
|
|
|
Site, Civil, Environmental: |
|
|
|
Landscaping: |
|
|
|
Topographic Surveying: |
|
|
|
Life Safety: |
|
|
|
Elevators: |
LBH Consulting |
|
|
|
|
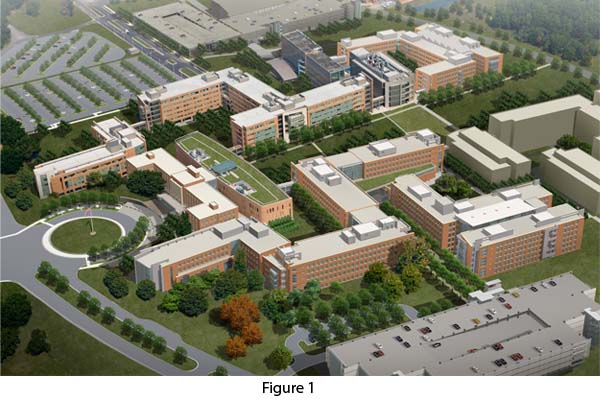 |
|
Architecture:
Starting the fifth phase of the consolidation efforts by the FDA, the OC/ ORA Office building plans to move the Office of Commissioner (OC), Office of Regulatory Affairs (ORA) Office building to the White Oak Campus. On the site of the former US Navy facility at the Federal Research Center- Naval Ordnance Laboratory, the OC/ ORA Office Building sits on the southern end of the site, and forms its shape around the existing buildings (Figure 1). Two Buildings compose the OC/ ORA Office Building. In Figure 1a Building 31 is circled and Building 32 is the remain of the Building. Looking at the plan of the building, it is broken up into four wings, Wing A through Wing D (Figure 1b). Building 31 is Wing A, and Building 32 is Wing B through D.
Forming a S shaped building, the 500,000 S.F. office building was laid out and designed to mirror the existing buildings on the site and to form a unique face of the campus from the main drive off of New Hampshire Ave. Building 31 and Building 32 are two buildings that are connected and considered mixed use. Main features in the office building are general office spaces, conference room space, and food service spaces. |
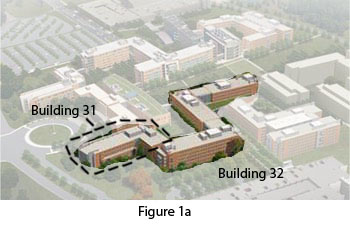 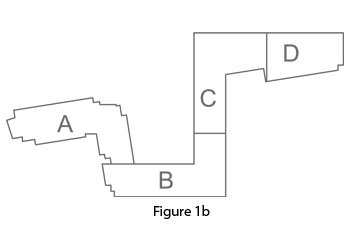 |
|
|
|
|
Building 31 Applicable Codes: |
GSA Facilities Standards for the Public Building Service
International Building Code 2003 (Excluding Chapter 10: Means of Egress)
NFPA 101, Life Safety Code, LSC 2003 for Means of Egress
Maryland Building Performance Standards, amended October 2001
Americans with Disabilities Act (ADA)
Uniform Federal Accessibility Standards (UFAS)
International Plumbing Code 2003
International Mechanical Code 2003
International Code Council National Electric Code 2005
International Fire Code 2003 |
|
|
Building 32 Applicable Codes: |
GSA Facilities Standards for the Public Building Service
International Building Code 2003 (Excluding Chapter 10: Means of Egress)
Life Safety Code 2003 (NFPA 101) for Means of Egress
Uniform Federal Accessibility Standards (UFAS)
National Electric Code 1999
International Mechanic Code 2003
Installation of Automatic Sprinkler Systems (NFPA 13) 2002
National Fire Alarm Code (NFPA 72) 2002 |
|
|
Zoning Requirements: |
No applicable zoning codes for government land. |
|
|
Historical Requirements: |
No historical requirements had to be met.
The white Oak Trees on the site were protected during construction. |
|
|
Building Enclosure |
|
|
|
Facade: |
The building enclosure that was designed for the FDA OC/ORA Office building is a Face brick veneer and curtain wall structure supported by a concrete frame (Figure 2). Building 31's primary glazing that was used was a vision panel glass unit. That is a 1 inch insulated glass unit with 13 mm airspace between the panels of glass. On the first floor of both Building 31 and 32 implement a curtain aluminum curtain wall system. An aluminum curtain wall system with shading devices integrated on the facade is on the west elevation of Building 31(Figure 3). At the atriums located throughout the building an aluminum curtain was system is designed for the facade (Figure 4). |
|
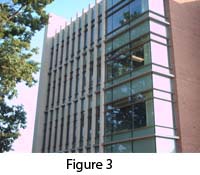 |
|
Roofing: |
The roofing system is a protected roof membrane assembly consisting of a hot fluid-applied membrane covered by insulation and ballast. A hot rubberized asphalt around 215 mils thickness is used as the membrane of the roof. Extruded polystyrene rigid board insulation of 80 mm thickness is the major insulation for the roofing system. White color solar and light reflecting ballast complying with LEED Requirements was used as the roofs top layer. Roof drains and overflow scuppers were provided on the roof to prevent any major water problems. Safety tieback anchors for window cleaning of the exterior and the interior of the atriums were installed on the roof.
On the Lower roof of Wing D and above one of the bridges is a Green Garden Roof (Figure 5). Garden roof manufacture recommended lightweight engineered soil, along with perennial plants that were select for resistance to temperature changes and anticipated rainfall for the project location.
|
|
|
Sustainability Features: |
Some features that were implemented into the building design were shading devices integrated into the building facade. A Garden Roof is implanted on the lower roof in the D Wing (Figure 5). Use of local environmental controls was designed along with the HVAC system. With the White Oak Campus being important to the community it was required to protect the white oak trees that fell within the site. A FDA OC/ ORA Office building in planned to achieve 32 LEED points and a possible up to additional 19 points that were listed as possible points. Primarily the points are from construction and material considerations. A few points were obtained from the HVAC system and the Indoor air quality section. |
|
|
|
|
|
|
Structural System: |
Building 31 utilizes a cast-in-place reinforced concrete structural system to resist the primary gravity that were required to be designed by code. The concrete strength for all concrete is 28 Mpa. Spread Footings were designed to rest on undisturbed soil or geopiers, noted by the geotechicnal engineer. Geopiers were placed beneath the spread footing were 95% compaction could not be met. Typical The footings range from 2100mm x 2100 mm to 3900mm x 3900mm. Column sizes for Building 31 are 600mm x 600mm and 400mm x 900mm. The building was designed for progressive collapse design. The exterior beams of each floor are the progressive collapse beams for the design. In the assembly space on the first floor 900mm x 1800mm post tension transfer girders were used to span the large opening. A post tensile force of 4540 kN is design for the post tension girders. A one way slab was designed for Building 31 that spans between the beams. There are ten different slab types ranging from 150 mm to 230 mm.
Two structural systems were designed for Building 32. In general the structure of Building 32 is cast-in-place reinforced concrete with a design strength of 28 Mpa. The columns loads are support by spread footings varying from 1400mm x 1400 mm up to 5000mm x 5000mm. Beneath the footings geopiers were used were the bearing capacity could not be met with the soil alone. The reinforced concrete columns span from the ground floor to the fifth floor with various sizes; 600mm x 600mm, 400mm x 800mm and 400mm x 1400mm. progressive collapse beams were also designed for Building 32 in accordance with code requirements for progressive collapse design. The interior beams are standard rectangular beams that transfer the load from the slab to the columns. A 250nmm two way concrete slab is the primary flooring system for the building. In the atriums located in Building 32 a steel structure is designed to support the high open areas. The column sizes for the Atrium are W200x35.9, W200X41.7 and W310x43. Connecting Building 32 to the CDER Office Building is a bridge with a concrete metal deck and steel framing (Figure 7 and 8).
|
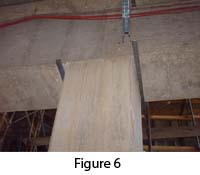 |
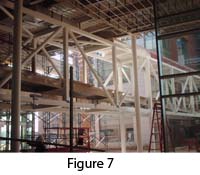 |
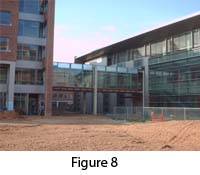 |
|
|
|
|
|
Lighting System: |
Throughout the building there are different types of spaces, having different lighting needs; typical offices, assembly space, food preparation areas. The typical office lighting with occupancy sensors is a florescent lighting system (Figure 9). Theatrical lighting is found on the first floor of A Wing in the Assembly space. Compact florescent down lights and line voltage halogen continuous run wall graze luminaries to provide uniform grazing on the vertical surface in the Assembly of A Wing. |
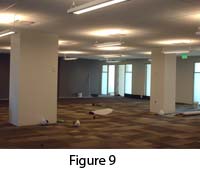 |
|
Electrical System: |
A Central Utility Plant (CUP) located on the campus serves utilities through the tunnel system under each building. From the CUP, 13.8 kV is supplied to the man in Unit Substation in Building 31. The Unit Substation feeds the switchgears in Wing A and D, the primary feed is 208Y/120V system for general use and 480Y/277 for lighting. Uninterruptible Power Supply systems (UPS) are located on various floors. No emergency power systems were designed for the building because the CUP provides unit erupted power |
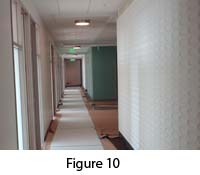 |
|
Mechanical system: |
The CUP provides hot and chilled water to Building 31 and Building 32. Building 31 has three AHU, two units on the roof and the third unit on the first floor. One of the roof top units is equipped with an enthalpy wheel for energy recovery. Building 32 is equipped with three roof top air handling units each equipped with enthalpy energy recovery wheels. The AHU operate with a Variable Air Volume System that has hook ups in the primary spaces, allowing the end user to monitor each space. A building automation system (BAS) is provided for the CUP to monitor various mechanical points throughout the building. |
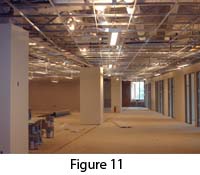 |
|
|
|
|
|
Construction: |
The site is located on fill, for the foundation to meet proper bearing capacity, Geopiers under the footers were used where the soil did not meet 95% compaction. Two bridges were designed that connected the FDA OC/ORA Office Building to two other existing buildings on the site. The two bridges being connecting to existing buildings required extra coordination between the FDA and Tompkins Builders.
For security reasons the office building is having interior finishes done from the top floor down. This allows the completed floor to secured and prevent any worker entering the space.
The tunnels located under the buildings that connect to each building had to be designed to allow for construction equipment and emergency crews to drive over the soil without damage the structure under the ground. |
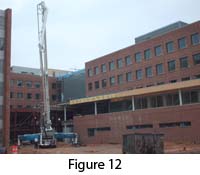 |
|
|
|
|
|
Fire Protection: |
The Building is equipped with a typical automatic wet sprinkler system. A Jockey pump is located in the tunnel of D Wing.
Type IB Fully Sprinkled Construction Type
2 hour fire ratings are provided for all exterior walls and exit stairways. The structural system must meet a 2 hour fire rating. |
|
|
|
|
|
|
Transportation: |
There are 5 elevator banks that house a total of thirteen elevators. Elevators 1 and 13 go to the tunnel level, the remaining elevators start on the first floor. |
|
|
|
|
|
|
Image source: |
Figure 1: Kling Stubbins in Association with RTKL
Figure 2-4: Pictures taken by student at site visit
Figure 5: Tompkins Builders
Figure 6-12: Pictures taken by student at site visit
|
|
|