General Building Information:
Name: Medical Office Building
Location: North-East United States
Occupant name: Unable to provide
Occupancy: New healthcare and business
Size: 72,706 S.F.
Number of stories above grade / total levels: 2 / 2
Owner: Anchor Health Properties
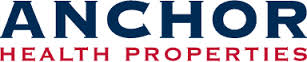
Architect: Array Healthcare Facilities Solutions
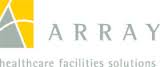
Civil Engineer: Nave Newell
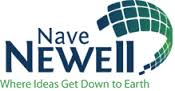
Structural Engineer: O’Donnell & Naccarato
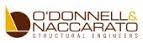
MEP Engineer: The Procz Group, Inc.
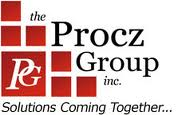
Equipment Planning: Sockwell & Associates
Dates of construction: May 2014 - May 2015
Cost: $21.9 Million
Building delivery method: Design-bid-build
Architecture:
The primary design goal of this building was to provide a building to house primary and specialty care physician offices, diagnostic imaging, physical therapy and laboratory services to an area that has experienced a large population growth in recent years. The building is located in an easily accessible area to all of the local areas and will feature a brick and metal façade with areas of textured glass.
Applicable codes:
International Building Code 2009
International Mechanical Code 2009
International Fuel Gas Code 2009
International Fire Code 2009
International Energy Conservation Code 2009
International Electric Code 2006
International Plumbing Code 2009
International Wildland – Urban Interface Code 2009
Accessible and Usable Building Facilities ICC 2003
Life Safety Code NFPA 2000
Health Care Facilities NFPA 2005
2010 Edition – FGI “Guidelines for Design and Construction of Health Care Facilities
Air Conditioning and Ventilating Systems 2002
The area that the medical office building will be built on is zoned as special limited business. The zoning code states that principal structures cannot exceed 75 feet and lot coverage may not exceed 70%. Building codes for this area also have limitations that the building height may not exceed 3 stories or 55 feet and the maximum square feet per floor may not exceed 86,250 S.F. According to the zoning code there are no historical requirements for this area.
Building Enclosure
Glazing:
There are four different types of glass that are used in this building, clear tempered, textured tempered, spandrel panel, and clear laminated. The clear tempered glass is used in a large section of curtain wall that encloses a feature set of stairs in the south end of the building. Clear tempered glass is also used in the sections of wall that have a large storefront window. This type of window is the most common throughout the building. In all of the storefront type windows there is a larger lower section of window that is composed of clear tempered glass and a smaller strip of glass at the top that is textured tempered glass. The spandrel panel is used near the roof where it sits above a two foot wide strip of textured tempered glass. A defining feature of the building is a pyramid shaped skylight that sits as the highest point on the building. The large square portion that the pyramid sits on is made of clear tempered glass with a strip of textured tempered glass. The pyramid itself is composed of clear laminated glass. This is the only location of clear laminated glass in the whole building.
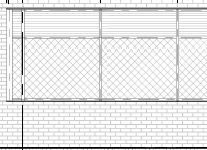
Courtesy of Array Architects
Building Facades:
The building façade is composed of brick, aluminum composite panels, glass, and a corrugated screen. On the first floor there are large sections of multi-layered glass previously explained in the glazing section. The areas that are not covered by glass are clad in brick. The overhang for the main entrance of the building is clad in aluminum composite panels. The second floor façade also consists of layered glazing like the first floor but instead of brick covering the remaining wall space, aluminum composite panels take the bricks place. To hide the mechanical equipment on the roof, a parapet wall is constructed using a corrugated screen.
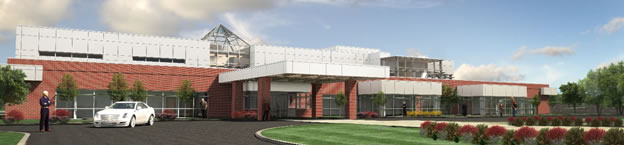
Facade rendering courtesy of Anchor Health Properties
Roofing:
The roof on the Medical Office Building will be a sloped flat roof. The slope will be achieved by a combination of tapered insulation and sloped steel framing. The roof covering will be an EPDM membrane. The roof will have several roof drains to provide relief for rain water.
Sustainability Features:
A feature employed to aid in sustainability is an economizer cycle built into the roof top units. This project also has area for rainwater management and the building was located on the site as to not disturb local wetland area. It is also noted that erosion must be controlled during the construction process as to not disturb local owners.
Systems Description
Mechanical Systems:
The Medical Office Building uses a very simple mechanical system for heating and cooling of the building. The building utilizes two roof top units with VAV reheat systems. The roof top units are self-contained as well as provide the necessary outdoor air required for the building. The building also has 5 ductless split system units to provide additional cooling to rooms that have a higher load such as the control room for the MRI machine.
Structural System:
The ground floor of the Medical Office Building will be a slab on grade system with 4” of concrete over 6” of crushed stone over 6mil of polyethylene vapor barrier. This is the same for the whole building except in the area of the mechanical room where the slab on grade will be increased to 6” of concrete.
The building will be steel framed with composite deck and concrete making up the floors. The concrete thickness will vary between 3 ¼” and 5” of lightweight concrete depending on the location on the floor plan. All connections to the columns will be flexible moment connections. The roof will be framed with metal deck on steel joists. The deck will then be covered with insulation and roofing membrane.
Lighting/Electrical System:
The Medical Office Building is fed by 3 #1/0 aluminum wires and 1 #2 ground wire supplying 35kV from the incoming service. It then goes through a 2500KVA transformer to bring the working power to 480/270V. There is also an emergency 600KW/750KVA generator to supply the fire water pump and other emergency devices.
The most abundant luminaires used in the building are 2’x4’ direct/indirect fluorescent fixtures and 2’x2’ direct/indirect fluorescent fixtures both manufactured by Daybrite. The building also makes use of LED fixtures and CFL bulbs to save on electricity.
Construction:
This building will be constructed under the design-bid-build method. The overall project budget is $21.9 million with $16.9 million going to the cost of construction.
Fire Protection:
The Medical Office Building fire protection will be a wet system with a pump to maintain pressure in the sprinkler pipes. It is also required that all openings in floors and walls will be fire stopped.
|