Building Statistics
Building Name: The Office Building
Location: Washington, DC
Occupant: Undetermined
Primary Occupancy Type: Office Building
Size: 108,000 SF
Number of Stories above Grade: 9 Stories
Primary Project Team:
Owner: Mid Atlantic Realty
General Contractor: James G. Davis Construction Company
Architect: Gensler
Civil Engineer/Landscape Architect: Wiles Mensch Corporation
Structural Engineer: Granzow Structural Engineers, PLC.
MEP Engineer: B&A Consulting Engineers
Vertical Transportation Consultant: Michael Blades & Associates
Dates of Construction: March, 2013 – March 23, 2015
Contracted GMP: $30.5 Million
Project Delivery Method: Design Bid Build
Architectural Design:
The architectural design consists of a single nine story tower above three levels of parking below ground, totaling roughly 108,000 square feet. The lowest level of parking holds an oil/sand separator for parking level drains, storm water sump pumps for parking level drains, as well as a fuel storage room. The first level of parking houses the main electrical room, along with the fire pump room and house pump room. The ground floor not only holds the main lobby, but houses open tenant office space like the second through ninth floors. A mechanical penthouse tops off the tower. The tower will have a glass and metal panel curtain wall, while the lobby will have an interior decorative glazed feature wall.
Figure 1 – Rendering courtesy of DAVIS
Architectural Function:
This building is comprised of open tenant office space and a few amenities. These amenities include a fitness center and locker rooms on the P1 level, and a rooftop terrace.
Code Requirements:
2006 IBC with 2008 DCMR 12A Building code supplement
2005 National Fire Protection Agency/National Electric Code with 2008 DCMR 12C Electric Code Supplements
2006 International Fuel Gas Code with 2008 DCMR 12D Fuel Gas Code Supplement
2006 International Fire Code with 2008 DCMR 12H Fire Prevention Code Supplement
2006 International Mechanical Code with 2008 DCMR 12E Mechanical Code Supplement
2006 International Plumbing Code with 2008 DCMR 12F Plumbing Code Supplement
2006 International Energy Conservation Code with 2008 DCMR 12I Energy Conservation Code Supplement
2003 American National Standards Institute 117.1 with 2008 DCMR 12A Supplements
Zoning Code Requirements:
2003 DCMR 11 Zoning Regulations, February
Historical Requirements:
There are no historical requirements for this building.
Building Enclosure:
The façade system on the north, east, and west elevations consists of low-iron tempered glass with minimal aluminum framing. The south elevation system consists of part low-iron glazed curtain wall and an insulated core metal wall panel system. The roof consists of forty percent terrace space with roof paver shown below in figure 2, and sixty percent green roof.
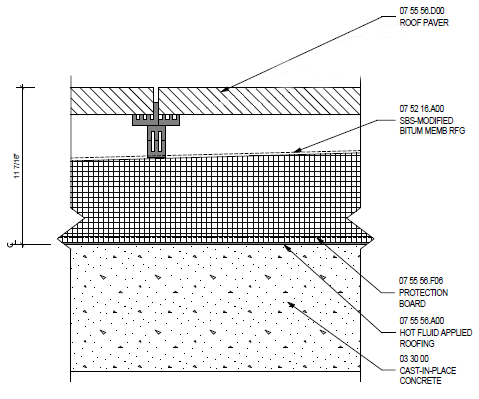
Figure 2 – Section courtesy of DAVIS
Sustainability:
This building is pursuing a certification of LEED Gold with its green roof mentioned above, its locally extracted and manufacture materials, its electric vehicle charging stations, and its recycled construction waste.
Demolition:
At the start of the project the site housed a nine story steel framed building. It was determined to build new instead of renovate the old, in order to meet the owner’s needs. With the demolition process, came the abatement of asbestos.
Structure:
The majority of the structure is cast-in-place concrete. The foundation system is comprised of a 5’ – 6” mat slab and micropiles. The floor slab thickness of the first and second parking decks and the first floor is 10”. Floors two through nine have a 9” slab. A 12” slab is used in the penthouse. An 8” wall encompasses the three levels of parking. The building will have a concrete structure with thirty by forty foot column spacing throughout. Most concrete will have a compressive strength of 4,500 psi, but the mat foundation will have a compressive strength of 5,000 psi and the below grade walls 6,000 psi. All concrete is to be normal weight, have a compressive strength of 7,000, and is to be post-tensioned. Fly ash and ground granulated blast-furnace slag will be used to replace up to 25% of the Portland cement.
The roof of the Penthouse and the rooftop trellis are the only sections of the building that utilizes structural steel and are comprised of both wide flanges and hollow steel square tubes. The use of steel above the Penthouse allows the roof to span over equipment without the need of columns.
Mechanical:
The Office Building utilizes a chilled water system to cool the spaces. Two chillers rest in the mechanical penthouse and make use of two cooling towers on the main roof. The chillers supply cooling to the two air handling units, also in the penthouse, which force air to separate air terminals on the second through ninth floors. These air terminals will supply the heating in the winter months. Along with the air handling units, the chillers supply water to variable air volume devices spread across the first floor for the retail space. All ductwork and mechanical piping is run through two mechanical chases by the restrooms.
Electrical:
This building uses a 120/208 V three phase distribution system. Service is provided by PEPCO at 120/208 V run into two separate 4000 amp switchboards. One switchboard feeds the parking floors through the fifth floor, and the other feeds the sixth floor through the penthouse and roof level. From the switchboards, bus duct is run up through the building where two sets of 4 number 3 wire act as feeder for the panels. There is also a 400 kW emergency generator designed for backup power to the fire pump, life safety systems, smoke removal systems, and elevators.
Fire Protection:
The fire suppression system is a wet sprinkler system with a siamese fire connection at the street level. Two hour ratings are mandatory for most assemblies, including shafts, exit passageways, exterior bearing walls, and the floor.
Support of Excavation:
This project has a very extensive support of excavation. With the proximity of the transportation tunnel so close to the site, the support of excavation does not have the ability for tiebacks. For this reason, cross bracing must be used across the site. To support the 20 inch diameter steel bracing, a ring of W24x104 steel wales will be installed. There will be two levels of wales and bracing separated by 22 ft.
|