User Note: While great efforts have been taken to provide accurate and complete information on the pages of CPEP, please be aware that the information contained herewith is considered a work‐in‐progress for this thesis project. Modifications and changes related to the original building designs and construction methodologies for this senior thesis project are solely the interpretation of Bryan Hart. Changes and discrepancies in no way imply that the original design contained errors or was flawed. Differing assumptions, code references, requirements, and methodologies have been incorporated into this thesis project; therefore, investigation results may vary from the original design.” |
|
|

BUILDING STATISTICS
General Building Data
- Building Name: Edenwald New Tower
- Location and site: 800 Southerly Road, Towson, Maryland 21286
- Building Occupant Name: Edenwald, a Continuous Care Retirement Community
- Occupancy type: Residential with amenities: 60 apartments and 32 assisted living units
- Size: 253,000 sq. ft.
- Number of stories above grade: 12
- Project Team:
- Dates of Construction: July 3, 2006 through March 27, 2008
- Overall Project Cost: $52 million
- Project Delivery Method: GMP (negotiated)
|
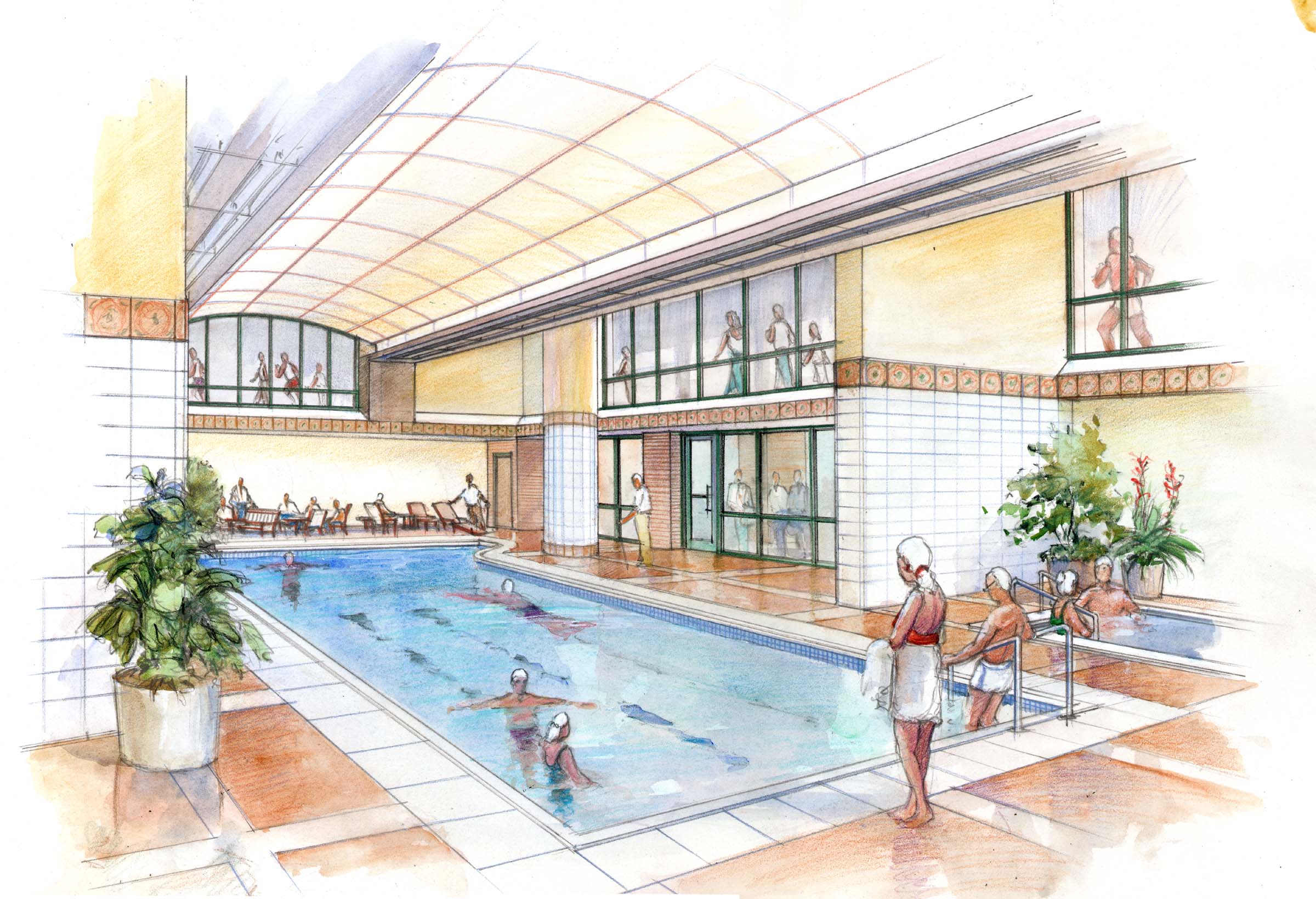 |
Architecture
- Design and Functional Components:
The Edenwald New Tower is a 12 story continuous care retirement community (CCRC) addition. It will house 60 independent apartment units and 32 assisted living units, in addition to 4 levels of parking. Amenities provided to the residents will include a large indoor pool, a whirlpool spa, a state of the art fitness center, fully equipped locker rooms, an enclosed, air-conditioned walking track, a spacious pub & lounge, and outdoor terrace to include a nine-hole putting green, and a chapel and great room.
The first floor of the tower will be contain most of the amenities, including the pool, health lounge, lobby, fitness center and chapel. Additionally, offices and the mechanical room will also be located on the first floor. The track will be suspended over the pool and entered through the second floor. The entire third and fourth floor will be devoted to parking, in addition to limited parking on the first and second floor. The apartment units will begin on floor 5, which will also contain the outdoor terrace and putting green, and continue through floor 12.
- Codes:
2003 International Building Code
2003 International Mechanical Code
1996 National Standard Plumbing Code
2002 National Electric Code
2003 International Energy Code
2003 NFPA 101 – Life Safety Code
2003 Edition NFPA 1 – Fire Prevention Code
COMAR 05.05.02, State of Maryland adopts ADAAG (Americans Disability Act) and FHAA (Federal Fair Housing Amendments Act of 1988) – Accessibility Code
COMAR 05.16.01 – Maryland Building Rehabilitation Code
Baltimore County Bill #08-05 – Fire Codes (local amendment)
Baltimore County Bill #01-05 – Building Codes (local amendment)
- Zoning:
The zoning for the tower at 800 Southerly Road is RAE 2 (residence, apartment, elevator).
- Historical:
Completed in 1985, the original Edenwald building was built on approximately 5 acres of land purchased from Goucher College. The existing high-rise structure is located in the heart of Towson, Maryland, and is one block away from Towson Town Center, providing residents with a great deal of opportunities within walking distance. The addition of the New Tower will increase the number of residents and provide new amenities to the complex.
- Building Envelope:
The Edenwald New Tower is enclosed with a combination of brick veneer, precast concrete panels, and glass windows and curtain walls. The roof utilizes a Firestone rubber roof with polyiso rigid foam board placed atop a post-tensioned concrete slab.
Building Systems
Structural
- Foundation:
The geotechnical analysis of the sub-surface conditions prior to construction revealed great variances in soil type and depth to bedrock, ranging from 50 to 150 feet deep, making deep foundations impractical. Given two recommendations from the geotechnical engineer, it was decided by the designers to use a geopier system as opposed to an alternative of driven HP 12x74 piles. Comprised of densified “rammed” stone aggregate piers, geopiers are referred to as “intermediate foundation systems” in that they strengthen, stiffen and reinforce soil layers beneath the building. The use of this option provided the opportunity to utilize a shallow foundation system of typical spread footings. (It should be noted, however, that pre-existing utilities only discovered upon excavation in the north end of the site required the use of the HP piles, in that localized area only.) The geopiers were determined to require a 30 inch diameter, and range from 20 to 30 feet in length. The allowable bearing pressure of the strengthened soil beneath the building was then determined to be 6 ksf beneath the tower, and 4 ksf beneath the parking garage. Total settlement expected from the geopier design amounts to one inch.
All concrete used in the Edenwald New Tower is normal weight (145 pcf dry unit weight). Footings, grade beams and slabs on grade have a minimum 28-day strength of 3000 psi. Shear wall footings have a minimum 28-day strength of 4000 psi. The slab on grade is reinforced with 6x6-W2.9x2.9 WWF on a vapor barrier on 4 inches of granular subbase.
- Floor System:
The typical floor system used is a 9 inch, post-tensioned concrete slab having a minimum 28-day strength of 5000 psi. In specific locations where the post tensioned system is not feasible and/or practical, reinforced one way slabs were used, ranging in thickness from 8 to 9 inches, with cast in place concrete beams, both requiring a minimum 28-day strength of 5000 psi.
- Roof System:
The flat roof system is almost identical to the typical floor system. Still utilizing the post-tension reinforcement, the slab thickness reaches up to 16 inches underneath the penthouse. The penthouse is supported by a steel braced frame and is covered by 1.5 inch deep, wide rib, 20 gage galvanized metal deck. The pentouse roof is supported by a combination of steel W shapes and 12k3 joists. The columns supporting the penthouse are W8x31 shapes.
- Columns:
The building is supported by rectangular concrete columns laid out in a geometric grid. The columns range in size, the most common being 22x22 and 22x36. The largest column found in the building is 22x60. Column loads range from 203 kips in the garage to 1600 kips at the base of the tower. From the ground level to the seventh floor, the columns are required to have a minimum 28-day strength of 6000 psi. From the seventh floor to the roof, that value decreases to 5000 psi.
- Lateral System:
The building is laterally supported in both the N-S and E-W directions by a total of 15 simply reinforced concrete shear walls, with thickness ranging from 12 to 14 inches. These shear walls are required to have a minimum 28-day strength of 5000 psi. Located throughout the building, the shear walls are often conveniently placed around stair and elevator shafts. All but one of the 15 shear walls run the entire height of the building.
Mechanical
The tower’s mechanical equipment is primarily located in two places: room 129 on the first floor, and the penthouse. The first floor mechanical room has two, 100-ton rotary screw chillers and a 9300 CFM air handling unit. The air handling unit features adjustable frequency drives for supply and return fans, which help energy savings. The mechanical room also features adjustable frequency drives for the two, cold water distribution pumps.
The penthouse features two, 51.7 BHP boilers, the pumps for which also feature the energy saving adjustable frequency drives. Next to the penthouse can be found the building’s 580 GPM cooling tower, provided with an 8kW electric basin heater. Also on the roof is an energy recover unit, which is estimated to recover 846.5 MBH on a winter design day, and 354.7 MBH on a summer design day.
Electrical/Lighting:
An external utility transformer in the northeast corner of the site provides 480Y/277 power to the building. Eight step down transformers provide 208Y/120 power for the apartment units. A 450 kW 480/Y277 emergency generator is located on the first floor. Though the entire building uses a wide variety of luminaires, the most common denominator is that most spaces are illuminated with fluorescent luminaires.
Fire Protection:
The entire tower is sprinkled throughout, while only the 1st and 2nd floor of the garage are sprinkled. Exterior bearing walls, exits and stair enclosures, shafts and elevators, the structural frame, floor/ceiling construction are all rated are rated at 2 hours. Dwelling unit separation is rated at 1 hour. The most restrictive travel distance is 250 feet with sprinkler.
Transportation:
Vertical flow of traffic is provided by four public elevators, one of which stops at the sixth floor, and two stairwells. Elevator access is provided to the parking garage.
|