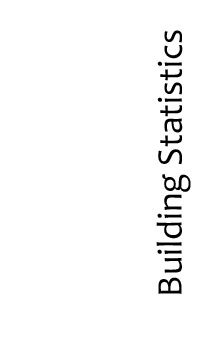 |
Building Name: City Center | Parcel 1 |
Location: Washington, D.C. |
Building Occupant Name: Multiple | office: law firm (undisclosed name) | retail: Apple |
Size: 257,500 sq. ft. |
Stories Above Grade: 12 |
Dates of Construction: 4/11 - 8/13 |
Cost: $45 million |
Delivery Method: Design-Bid-Build |
|
Owner: Hines |
GC: Clark-Smoot |
Architect: Foster + Partners |
Civil Engineer: Delon Hampton & Assoc. |
Structural Engineer: SK&A Structural Engineers with Thornton Tomasetti Group |
MEP Engineers: TOLK, Inc. |
Electrical Contractor: Truland |
|
|
|
Architecture |
City Center D.C. is a 2.5 million sq. ft. mixed-use development on a 10-acre site in downtown Washington D.C. It takes the place of the old Washington D.C. Convention Center, and consists of 2 condominiums, 2 rental apartments, and 2 office buildings. The goal of the city was to develop this part of the community in the best interests of its inhabitants. Retail stores, restaurants, and public gathering places will be incorporated into the design via the first floors of the buildings and the inner courtyard. Two new streets will be introduced in between the development, as well as a small park across the street. All of the structures sit on top of a 4 story garage that spans the entire site, connecting the development. Delivery systems are all underground in this garage, eliminating the need for exterior access points.
The building of interest for this report is one of the two office structures. It is a 12 story, 257,500 sq. ft. high rise office building with a curtain wall exterior. It is rectangular in shape, with flush curtain wall facades on each side. It is identical to the adjacent office building, and is actually connected via several catwalks. The interior design is currently being reworked due to the newly acquired tenants, who requested a brand new design. The architects concentrated on creating a design that would both fit into the surroundings and stand out as a high-end building. All 6 of the buildings on the development embrace the curtain wall dominance and align with each other to create unity.
IBC, 2000 edition
DCMR 11 – Zoning Regulation
DCMR 12 Building Code Regulations 2003 Edition
International Energy Conservation Code, 2000 Edition
International Mechanical Code, 2000 Edition
NFPA 70, National Electric Code, 1996 Edition
International Plumbing Code, 2000 Edition
International Fire Code, 2000 Edition |
|
|
|
|
|
Building Facade:
The building façade of the office building is entirely curtain wall. It is identical on every floor and wraps around the entire building. Insulation is included in the curtain wall assembly. The curtain wall system is supported via embed plates in the slabs. The curtain wall runs from slab to slab and clings on at these connection locations. The catwalks that connect the two buildings are made of the same curtain wall. Depending on the tenants for the retail space, some small color variations may occur on the first floor.
|
|
Photo - Andy Penev |
Roofing:
There are 6 typical roof system types. These range from green roof to stone to wood decking, depending on the roof space utilization. (A mechanical penthouse resides on the roof, surrounded by green roof.) See details below.
|
|
|
|
|
Sustainable Features |
The green roofs, plant materials, and construction materials were carefully planned for this project. The plant materials are native and adaptive to the environment. For construction, each material was considered for ease of assembly and location. Water management systems exist throughout the entire development, from the green roofs to the landscaping. LEED Gold certification is anticipated for this project. |
|
|
|
|
Structural |
Structural Steel Frame
The only sections of the building that utilize steel construction are the atrium and mechanical penthouse. The atrium, which extends the entire height of the building, is composed of W and HSS beams. An enclosed curtain-wall bridge, also composed of various W beams, connects the atriums of each building. The penthouse mezzanine and roof framing are also composed of W beams, ranging from W10 to W18. This is due to the heavy loads associated with the mechanical equipment. Also, by using steel beams, more space is allotted for openings, chases, and cores in between the beams, whereas the typical post-tensioned slab would have reinforcement that would interfere. If concrete beams were to replace the steel beams, they would have a much larger depth because of the loads, and as a result, take away from the ceiling height on the lower level. Structural steel framing is used on each floor at the core of the building, to enclose the bathrooms, mechanical, electrical, and storage spaces.
Cast-in-Place Concrete
The majority of the structure, including the floor slabs, drop panels, columns, and shear walls are cast-in-place concrete. Typical on every floor are 8” thick post-tensioned slabs with 6” drop panels at the columns. Formwork for the slabs consists of No. 2 lumber and plywood, supported by traditional shoring. Temporary steel beams support the plywood and lumber, where the rebar and post-tensioning cable are arranged on stools. The crane hoists buckets to the desired location and the slab is poured and formed. A concrete batch plant was set up due to the extremely large demand for concrete for the entire project. The addition of this plant eliminated the travel time for trucks, and fresh concrete was more readily available.
Underneath the office building is a four-story garage. As a result, the first floor slab includes rigid insulation between the garage roof slab and the office building first floor slab. This was done in order to reduce the noise from the garage below and minimize the heat loss through the floor. The foundations of the office building tie into the parking garage structure, which was designed to carry the loads of all 6 buildings. |
|
|
|
|
Mechanical |
The office building utilizes a chilled water system to provide cooling to the spaces. A chilled water air handling unit is located in the mechanical room on every floor of the structure. Outside air, along with return air, is cooled via chilled water coils and circulated to the fan powered terminal units. Each floor is separated into zones to provide optimal control for the user. Due to the lack of walls, the multiple FPTUs have been designed to allow tenants to control and condition zones of the floor differently. Electric heaters in the AHU and FPTUs provide heat to the space during the winter months. The AHU on each floor is located in the core, with the pipes and ductwork webbing out to the remaining space. Three cooling towers, outside air handlers, and several other rainwater filtration systems are housed in the mechanical penthouse on the roof of the building. |
|
|
|
|
Electrical |
City Center Parcel 1 uses a 480/277V electrical distribution system. Service is provided by PEPCO at 480/277V, run through a utility meter, and into the switchboards. The two office buildings share an electrical room on level B1, the uppermost level of the garage. There are four switchboards, 2-3000A and 2-4000A. Each 4000A switchboard feeds the electrical closets on every floor of its respective building via a 4000A busway. The remaining two switchboards are shared between the two buildings. 480/277V to 208/120V step-down transformers are located in each electrical closet and at every location that requires lower voltage. This allows runs to floors to have smaller wire sizes due to the higher voltage feeders. In the case of interrupted or lost service, there is a 750kW standby generator designated for backup power to the fire pump, life safety systems, smoke removal systems, equipment, and elevators. Automatic transfer switches are used to detect outages and relay to the generator. |
|
|
|
|
Fire Protection |
Fire suppression for this office building is quite extensive, due in part to the high-rise classification. Smokeproof/pressurized stairways, sprinklers, and fire dampers are utilized throughout the building. Two hour ratings are mandatory for most assemblies, including shafts, elevator hoistways, exit passageways, the structural frame, and the floor. |
|
|
|
|
Transportation |
There are 5 elevators and 1 service elevator located at the core of the office building. Enclosed catwalks connect Office Building 1 with Office Building 2. |
|
|
|
|
Telecommunication |
As of
09-Jan-2013
,
the telecommunication systems are yet to be designed for Office Building 1. It is anticipated that the future systems will be extensive. |
Note: While great efforts have been taken to provide accurate and complete information on the
pages of CPEP, please be aware that the information contained herewith is considered a work in
progress for this thesis project. Modifications and changes related to the original building designs and
construction methodologies for this senior thesis project are solely the interpretation of Andy Penev. Changes and discrepancies in no way imply that the original design contained errors or was
flawed. Differing assumptions, code references, requirements, and methodologies have been
incorporated into this thesis project; therefore, investigation results may vary from the original
design. |
This page was last updated on
January 9, 2013
, by Andy Penev and is hosted by the AE Department ©2012 |
|