Building Name: Washingtonian Center
Location: 9711 Washingtonian Blvd, Gaithersburg Maryland 20877-5359
Site:
The building sits on a site of approximately 8 acres, located between Interstate 270 and Washingtonian Boulevard. The Washingtonian Center will eventually be nestled between another office building that and a parking garage to serve the two buildings. The garage will be built in two phases, the first corresponding to the construction of the Washingtonian Center and the second along with the construction of the second office building at a yet undetermined date. See image below.
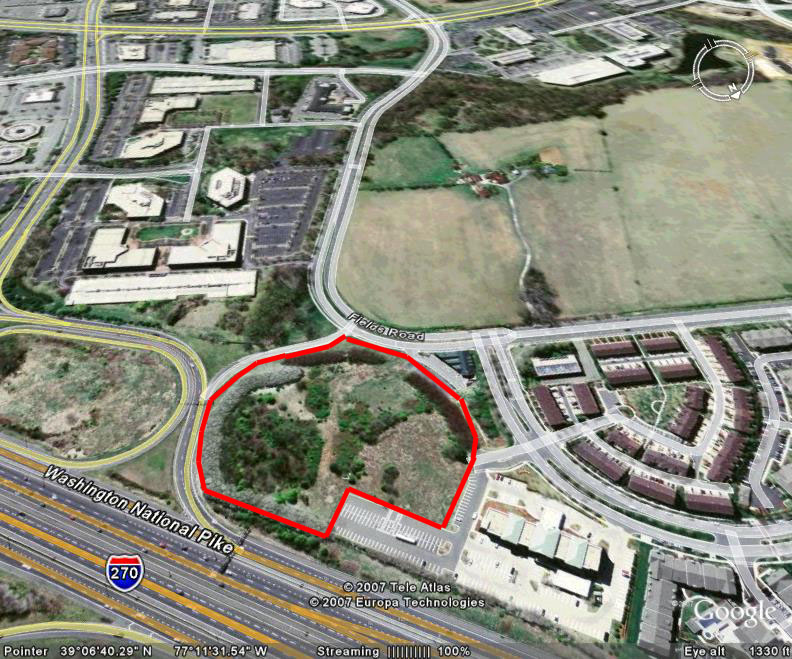
Occupancy Type: Office Suites for yet to be determined tenants.
Size:
Floor Square Feet
1 24,500
2-6 24,985
7-8 24,877
Total 199,164
Height: 8 stories with a mechanical penthouse on the roof. 107’-4” Tall at highest elevation.
Project Team
Owner: Washington Property Company
Architect: Wisnewski Blair and Associates LTD
Landscape Architect: Lewis and Scully Gionet
Structural Engineer: Echelon Engineering
M.E.P. Engineer: GHT Limited
Civil Engineer: Rodgers Consulting, Inc.
Construction Manager: Yet to be decided
General Contractor: Yet to be decided
Project Delivery Method: Design, Bid, Build
Architecture:
The Washingtonian Center is styled in a typically modern fashion with a simple form and virtually no ornamentation. Its styling lends itself to the function of the building, making it instantly recognizable as an office building. The exterior of the building is clad with a curtain wall façade and pre-cast paneling. The building was designed in a way to make the leasable space as flexible as possible to accommodate the needs of all future tenants. The core and envelope of the building will obviously be provided along with the common amenities such as the restrooms and elevators, while the specifics and finishes within the leasable space will be left to the tenants.
Major National Model Codes:
- 2003 International Building Code
- 2003 NFPA 101
Zoning: Commercial
Historical Requirements of the Building or Zone: Nothing noteworthy, the site is a new previously undeveloped location.
Building Envelope:
The building envelope for the Washingtonian Center is composed of a glass curtain wall façade, with steel mullions and pre-cast concrete panels. There are three typical sections in the envelope of the building. The first occurs at the entrances of the building where the curtain wall steps back at the second floor to set the entrance apart from the rest of the façade and also to accommodate the two story entrance into the building. The only pre-cast paneling at such sections are horizontal pieces at the second story where it steps back and at the roof of the building. The second section in the curtain wall is nearly the same as the first however there is no step back in the façade. This condition happens at the four corners of the building. The final section in the envelope has the same glass curtain wall but instead it is now set off with pre-cast paneling for the entire height of the building. In this condition the bottom two floors and the upper two floors are grouped together in within a single assembly of pre-cast paneling while the four other floors each have their own assembly of panels. See the image below for a visual representation of the three building envelope sections.
In all cases the glass curtain wall is connected to the structure with an anchor that is embedded into the floor slab at each story. The pre-cast panels are attached with anchors that are embedded into the panel themselves and then bolted or welded to the steel structure at the appropriate locations.
The roofing system is 22 gage non-composite steel roof decking with a concrete topping. The decking is supported by steel beams and girders. The roof system is the same for the building and the mechanical penthouse roof.
Structural Systems:
The building is supported on spread footings ranging in size from 5’ squares on the exterior column lines, to 11’ squares supporting interior columns. The footings range in depth from 18” to 36”. The lateral frames of the building rest on two large combined mat footings measuring 32’ by 40’ and are 4’-6” thick. The base plates for the columns are typically 1.5” thick and 18” squares. A steel frame consisting of columns, beams and girders supports the building. The columns are spliced at the fourth and seventh floors and range in are typically W12 x 87on the first floor and W12 x 53 at the roof. Beam sizes are W21 x 44 featuring 1.5” inches of camber for the longer spans of 43’, and W 14 x 22 for the short spans of 20’. For the gravity frame system connections are all shear type and typically double angles for both a column to beam connection and beam to girder connection with the beam using a top coop. The lateral forces acting on the building are resisted by braced chevron frames enclosing each of the two elevator cores on two sides. Theses braced frames feature columns that are again spiced at the fourth and seventh floors and are W12 x 210 at the base and W 12 x 65 at the top of the building. The connections for the braced frame are done with gusset plates welded to the beams and connected to the angled braces with double angles and a web plate on each side. The floor system for the building is 3”, 20 gage steel composite floor deck with 3-1/4” topping of lightweight concrete. Composite action is provided by ¾” diameter shear studs welded to the decking.
Mechanical System:
The mechanical systems are all electrical powered and most of the main equipment is located in the mechanical penthouse on the roof. Fresh air is supplied to the buildings system by an outdoor air unit on the roof, which is capable of delivering 26,600 CFM of fresh air. The outdoor air is pre-conditioned by passing through an enthalpy wheel that transfers thermal energy from air being exhausted to the new fresh air entering the building. Each floor has a water-cooled A/C unit that services that particular floor. The first floor has an addition one of these units for both the fitness room and the lobby. Each floor’s A/C is capable of approximately 1050 Mega BTU of overall output. The refrigerant for these units is cooled by passing through a cooling tower located on the roof of the building. The air is distributed into the spaces passing through parallel fan powered terminal units where it can be heated as necessary. There are also variable air volume boxes that control the flow rates delivered to the tenant spaces.
Plumbing:
The plumbing system is contained mainly in the plumbing room located on the first floor of the building. An external connection to the water and sanitary lines occurs on the north face of the building. Hot water is provided for the building by water heaters with a capacity of 120 gallons, located on the first, second and sixth floors. System pressure is provided by a triplex domestic water booster system. The water and waste is moved vertically through one of three wet-stacks located in the men’s and woman’s bathrooms and in the plumbing room. Rain water collected by the roof drains passes through the roof and into one of the wet-stacks through a 4” pipe.
Electrical:
The building is serviced by a 12.47 KV electrical feed. A 30 KVA UPS system distributes power and services all the electrical systems in the building. The building uses both 480Y/277 volt and 208Y/120 volt distribution systems. A four cycle diesel powered emergency generator producing 600 KW of continuous standby power at 277/480 volts maintains vital building electrical systems, including one elevator, in the advent of a blackout. The elevators in the building use a three-phase 600A frame with a 65,000 RMS symmetrical amp rating. The main distribution switchboard is located on the first floor. Each floor has its own 75 KVA transformer and panel board controlling that floor.
Lighting:
Outdoor Lighting
Canopy Lighting over Building Entrances-Side-mounted white LED down light, 1 watt, 120 volts
Doorway Lighting-Wall-mounted full cutoff compact fluorescent area light, 277 volts
Parking and Road Areas-Pole-mounted full cutoff metal halide area light with integral magnetic ballast, 250 watts, 277 volts
Front Plaza-Pole-mounted metal halide asymmetric area light with indirect up-light detail, 70 watts, 277 volts
Indoor Lighting
Tenant Area Lighting-Recessed fluorescent T8 lamps, 18 watts, 277 volts
Construction:
The construction on the Washingtonian Center has yet to begin. The building is currently in the bidding process for a construction and management.
Fire Protection:
The building is one hundred percent fully sprinklered using an automatic wet-pipe system for all indoor spaces. Outdoor spaces will utilize a dry pipe system. Fire department stand pipe connections are made on the outside of the building with interior standpipe connections occurring in the stairwells are each floor. Portable fire extinguishers will be provided and installed through out the building. The structural steel will be coated with fireproofing to meet specific code required fire ratings.
Transportation:
There are four entrances into the building. The main entrance is located at the center of the west face of the building. This enters directly into the double heighted lobby. Passing straight through the lobby a second entrance serves the east face of the building. Additionally there is a third entrance to the building at the end of the hallway branching off of the lobby. The tenant spaces in the building are served from the four elevators that are assessable directly from the lobby. Each has a load capacity of 3,500 pounds. There are also two stair cases located in the central core with fire rated hallways providing exist to the outside.
Telecommunications:
The future tenants of tenants of the building will install their own telecommunications systems to meet their specific needs. |