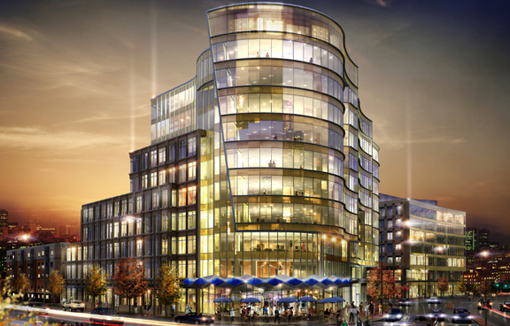 |
|
800 NORTH GLEBE
ARLINGTON, VA |
RYAN JOHNSON / ARCHITECTURAL ENGINEERING / STRUCTURAL OPTION |
building statistics |
|
general building data |
|
building name
|
|
800 north glebe |
|
location and site |
|
glebe road
arlington, VA |
|
occupant |
|
up for lease |
|
occupancy type |
|
mixed use offices |
|
size |
|
316,000 sf |
|
number of stories |
|
10 stories + 1 penthouse and 3 below grade parkiing |
|
constructon dates |
|
2011 expected
delivery date |
|
project delivery method |
|
design-bid-build |
|
contract type |
|
at risk |
|
project cost |
|
$62 Million |
|
ARCHITECTURE
800 North Glebe is a 10-story 316,000 square-foot trophy mixed-use office building. Retail and public gathering spaces are located at street level in the 2-story lobby of the building. The remaining nine levels will provide class-A mixed-use offices. 800 North Glebe was designed for LEED Gold Certification by utilizing numerous strategies to minimize its carbon footprint.
The 10-story façade, created by three sail-like sweeping glass curtain walls, accentuate the sight lines of the building. Radial lines and circles were widely used to define the crown and drum feature of level one and the sail feature of the remaining levels. Building setbacks are located at level four, six and eight to give dimension to the building. Refer to figure 1 for visual representation of façade features.
Retail and community spaces on the ground level offer 14’-6” ceiling heights with floor-to-ceiling glazing. Over the main building entrance, there is a diamond expression decorative composite metal canopy with a plaster soffit and sunguard ultrawhite laminated backlit glass. See figure 2 for visual representation. Offices on levels two through eight have 9’-0” ceiling heights, with the remaining two levels will have 10’-0” ceiling heights. A 3-level parking garage is shared between 800 and 900 North Glebe which offers ample parking at a ratio of 1/580 RSF.
Numerous amenities are included on-site and within close proximity of 800 North Glebe. Multiple retail options, restaurant with fresco seating, a café with outdoor seating and fitness center are integrated on-site. The superb location features offsite amenities within a short walk, including Westin Hotel, Ballston Common Mall, and Ballston Metro stop. These locations offer sit-down and casual dining, Reebok Fitness Center with indoor pool, business conference room, retail shops and a movie theatre. For those that choose to be outdoors, a dedicated jogging and biking trail is located in the area.
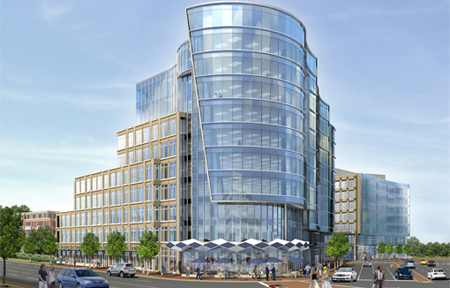
|
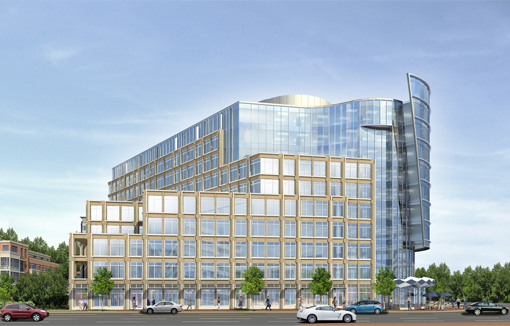 |
applicable zoning and codes: |
|
zoning: |
2007 arlington county zoning ordinance |
|
building: |
2003 ibc, 2003 virginia usbc |
|
life safety: |
nfpa 101 life safety code, 1985 |
|
fire alarm: |
nfpa - 72/1999 |
|
sprinkler: |
nfpa - 13/1999 |
|
mech/gas/plumbing: |
2003 icc |
|
electrical: |
2002 nfpa national electric code |
|
energy: |
2003 icc |
|
elevator: |
ansi/asme a17.1, safety code for elevators/escalators |
|
handicap: |
ansi a1 17.1, provide accessibility & usability for physically handicapped people |
|
|
|
BUILDING ENVELOPE
fascade:
Three types of Architectural precast panels, metal cladding and glazing will adorn 800 North Glebe’s façade. The large sail-like curtain wall consists of Viracon VRE 1-46 on insulated heat strengthened vision and spandrel glass with PVD finished custom color composite metal mullions. Along the street level, one will find a variety of stone, metal and glazing. These include Oconee granite with a polished finish at the base, insulated spandrel glass, precast concrete panels with a light sandblast finish and PVDF finished aluminum louvers.
Vertical bands rising up the building are made up of precast concrete panels with a medium sandblast finish while horizontal bands consist of exposed aggregate finished panels. Other glazings found on the building are sunguard supernatural-68 on ultrawhite insulated glass and Viracon VRE 1-46 on insulated punch vision glass. |
roof:
Protection from the elements on the roof is provided by the composite roof membrane. The composite consists of R-19 high density rigid insulation, protection board, and fully adhered 60 mil TPO membrane on top of a structural concrete slab. Where the roof system terminates at a curtain wall, fluid applied waterproofing is placed atop drainage board.
|
|
|
SUSTAINABILITY
Innovative sustainable and responsible design practices are one of the designer’s primary goals. Integration of sustainability and every day design by minimizing the carbon footprint, balancing energy and resources and feasibility all went into the design on 800 North Glebe. In accordance with the U.S. Green Building Council’s Leadership in Energy and Environmental Design, the owner has a goal to achieve LEED Gold Certification, which the designers fulfilled. LEED Gold Certification requires the design to attain at least 34 out of 61 possible points.
A breakdown of anticipated points:
Sustainable site: 10/15 of attempted
Water efficiency: 3/5 of attempted
Energy and atmosphere: 5/14 of attempted
Materials and resources: 3/11 of attempted
Indoor environmental quality: 9/11 of attempted
Design process and innovation: 4/11 of attempted
|
|
STRUCTURAL SYSTEM
Substructure:
Geotechnical studies performed by ATC Associated Inc. reported site and subsurface conditions encountered details their geotechnical recommendations for the project. Three levels of parking make up the substructure of 800 N. Glebe at roughly thirty feet below existing grade. Analysis indicated that spread footing foundations would be the most feasible for a majority of the structure. However, under interior wall and column footings the foundation be designed with minimum widths of 18” to 24”. Under the ground level lobby area, caissons needed to be a minimum diameter of 60” and a mat foundation would be sufficient when designed for a maximum allowable bearing pressure of 3.5 ksf.
3 ksi normal-weight concrete (NWC) is used for the foundations and interior slab on grade, the garage SOG uses 4.5 ksi NWC and the cellar columns are composed of 4 ksi and 8 ksi. Reinforcing varies in size throughout the footings and caissons, depending on thickness.
Superstructure:
One-way slab for the ground level retail include 10” thick slabs with 10’-0”x10’-0”x5.5” drop panels. Plaza slabs are 12” thick with 10’-0”x10’-0”x12” drop panels. Concrete strengths for the ground level include 3 ksi (SOG), 5 ksi (plaza slabs and framed interior slabs) and 4,6 & 8 ksi (superstructure columns). Post-tension design allowed for greater bay sizes of 30’x46’. Greater bay sizes offer more efficient floor plates (30,000 SF) for the tenant. Girders range in size from 48” wide x 18” thick to 72” wide x 20” thick. For levels two through six, two-way mildly reinforced slabs and one-way slabs over post-tension girders are implemented. Above level six, the superstructure consists of only one-way slabs over post-tension girders. Two-way slabs are 10.5” thick and generally reinforced with #5 @ 10” in both directions. Drop panels in these areas are typically 10’-0”x10’-0”x7.5” to alleviate punching shear at the columns. Slabs over the 36” diameter column are 12” thick with #5 @ 12” parallel to the girder and #6 @10” perpendicular to the girders, due to the cantilever action.
Lateral System:
Shear walls in the core of the building provide the entire lateral support. Two 12 in thick “C” shaped walls, 31.83’ long East/West and 9.58’ North/South per each “C”, encasing the elevator banks, reinforced with #4 horizontally and #5 vertically. From the sixth floor down, walls running North/South are specially reinforced three feet from each end with #7 and #8 rebar. Great care was given to limit the size and number of shear walls so as not to modify the floor layouts.
|
|
MECHANICAL SYSTEM
Nine 30,000–37,000cfm air handling units are located throughout the building, one per floor on levels two through ten. All units are variable air volume systems with electric heat allowing for zone variations throughout each floor. On the roof are three large cooling towers, each with an 800 gpm capacity. One of the heat exchangers offer a chilled water free cooling capability, allowing the system to bypass the two water cooled centrifugal chillers.
|
|
LIGHTING / ELECTRICAL SYSTEM
The electrical system used to power 800 North Glebe is controlled by 480/277/V 3-phase 4-wire system carried by a 3000A busway. The utility service room is located in the Northwest corner of the first and second parking levels of the garage. An emergency generator can provide 450 KW of power to emergency lights, fire pump, sump pumps and stairwell pressurization fans through a 480/277V 3 phase system.
There are a variety of lighting fixtures used on the site. The electrical consultant recommended using fixtures that utilized MR16 types lamps, with remote transformers where required. All exterior fixtures are wet rated. Interior fixtures included are surface mounted F32T8s, wall mounted CFLs and recessed F28T5s. Occupancy sensors are to be installed on all office levels, but may be manually overridden by wall switches.
|
|
CONSTRUCTION
Construction began with excavation for the three level parking garages that will service 800 North Glebe, 900 North Glebe and the AHC housing complex. Expected completion for the building is 2011 and a total cost of $62 million dollars. Design-bid-build is the project delivery method with a at risk contract type. Clark Construction is the leading contractor on the job.
|
|
FIRE PROTECTION
Fire protection is compliance with the latest city of Alexandria fire protection code reference package. Emergency system statuses are controlled by zones on each level, 2 per level of floors 5 through 10 and 3 zones for the ground level. Four inch standpipes are located stairwells A, B and D supplying water to all superstructure levels, along with the three below grade parking levels.
|
|
TELECOMUNICATIONS
Telecommunication for the building includes 4 4” sleeves per floor connected together through the telecommunication bonding backbone. The main telecommunication room is located on the first parking level of the garage.
|
|
TRANSPORTATION
Nine elevators and four stairways provide vertical egress for 800 North Glebe. Eight elevators and a pair of stairways are centrally located in the core of the building. Stairs A and D continue from parking level 3 and continue to the tenth floor while two elevators service the cellars to ground level and the remaining six elevators service the remaining ten levels. Above level ten, stairway A becomes a maintenance egress to the penthouse where the elevator control is located.
Away from the central core there are two stairways and one elevator. Located in the northwest corner, stairway B services the ten tenant levels of 800 N. Glebe and a retail elevator services the three levels of parking garages. The final stairway, found outside of the superstructure, gives egress for the cellars to the ground level. |
|
|
Special thanks to The JBG Companies for use of renderings from 800northglebe.com
User Note: While great efforts have been taken to provide accurate and complete information on the pages of CPEP, please be aware that the information contained herewith is considered a work-in-progress for this thesis project. Modifications and changes related to the original building designs and construction methodologies for this senior thesis project are solely the intrepretation of Ryan Johnson. Changes and discrepencies in no way imply that the original designed contained errors or was flawed. Differing assumptions, code references, requirements, and methodologies have been incorporated into this thesis project; therefore, investigation results may vary from the original design.
This was last updated on
October 15, 2009
by Ryan Johnson and is hosted by the AE Department © 2009 |