Building Statistics
Part I
___________________________________________________
Building Information
Building Name |
South Halls: Ewing-Cross Renovation |
Location and Site |
The Pennsylvania State University, University Park, PA 16802 |
Building Occupant Name |
Penn State |
Occupancy Type |
Mixed Use Residential R-2/Assembly A-3/Storage S-1 Separated |
Size |
71,002 GSF |
Number of Stories Above Grade |
4 Plus Basement |
Construction Schedule |
May 2013 - December 2013 |
Overall Project Cost |
$94.1M |
Phase Project Cost |
$15.2M |
Project Delivery Method |
Design-Build |
Project Team
Primary Project Team
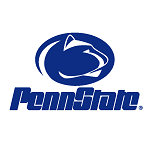 |
Owner: The Pennsylvania State University |
|
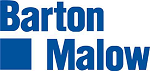 |
Design Builder: Barton Malow |
|
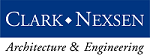 |
Architect/Engineer: Clark Nexsen |
|
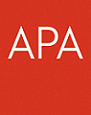
|
Local Architect: AP Architects |
|
|
Civil Engineer: Sweetland Engineering & Associates |
|
Specialty Contractors
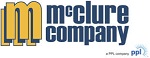 |
Mecanical & Plumbing: McClure Company |
|
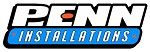 |
Exterior Framing & Drywall: Penn Installations |
|
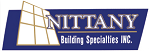 |
Glass and Metal Panels: Nittany Building Specialties |
|
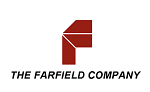 |
Electrical: The Farfield Company |
|
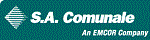 |
Fire Protection: S.A. Comunale |
|
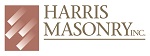 |
Masonry: Harris Masonry |
|
Project Location
Figure 1: Birds eye view ~ Bing Maps
Architecture
Design
The South Halls Renovation and Construction is located on the University Park campus of the Pennsylvania State University. Along with the Haller-Lyons dormitory, Ewing-Cross comprises Phase 1 of the South Halls renovation project. Ewing-Cross is four stories plus basement; the two wings of dormitories are connected by adjoining stairwells and a common lounge. The renovation includes the demolition and construction of MEP systems, as well as a façade facelift which features limestone veneer stone panel projections and new low-e glazing. The overall architectural design of South Halls stays in line with the rest Penn State’s campus, by featuring a brick façade with limestone. Ewing/Cross features 130 student bedrooms, 9 sorority suites, and 4 stacks of private bathrooms.
Building Facades
Clark Nexsen implemented three different types of building facades for Ewing/Cross. The first type of building envelope is the existing brick veneer, which ties into a CMU wall; 1-1/2” rigid insulation along with 6” batt insulation was added to the interior of the CMU wall to improve the building’s heating/cooling efficiency. The second wall type is the stone panel system. 6” metal studs tie directly into the existing brick veneer to support the 1/4" stone panel system.
Ewing/Cross also features aluminum frame window and glazing. The curtain wall system designed for Ewing-Cross follows the same scheme as the existing curtain wall at the stairwells. The curtain wall works to allow natural light to penetrate the stairwells for both Ewing and Cross. Aluminum frame storefront and insulated low-e double pane glass are the two components of the curtain wall system. The aluminum framing and metal trim is designed to match the rest of the storefront and window trim. The low E glass will help to reduce the building heat loads as well as earn LEED credits.
Figure 2: Facade Locations - Quaid Spearing
Building Roof
There are two different types of roofing systems used on Ewing/Cross. The first is a single ply EPDM roofing membrane over rigid insulation; the EPDM is utilized on the flat roof surfaces that cover the meeting rooms and wrap around porch. The second type of roofing system is a shingled roof with recycled rubber and plastic slate shingles. In comparison to the slate shingles which are typically used on campus buildings, the rubber shingles were chosen because of their cost savings and durability, while still retaining the look of slate shingles.
Sustainability Features
The South Halls project is aiming to achieve a LEED Certification but is tracking to achieve LEED Silver Certification. The project follows the LEED 2009 for New Construction and Major Renovations and is currently able to achieve 47 points, in the various categories. Some LEED categories include sustainable sites, water efficiency, materials and resources, indoor environmental air quality and innovation in design process. The rubber and plastic shingles mentioned earlier make use of recycled rubber from old tires. Additionally, several of the sustainable devices integrated into the project’s design include: increased insulation values at the exterior walls, low e pane glazing, daylighting, low VOC materials and the use of recyclable materials.
One of the more notable sustainability features are the two energy recovery ventilation units (ERV), which extract energy from the air exhausted out of the building and use it to treat the incoming outdoor ventilation air. The ERVs will help to reduce energy consumption while meeting ASHRAE 62.1 standards and achieving LEED points in the Energy & Atmosphere Credit 4.
Major National Codes
According to the International Building Code, Chapter 6, Table 601 Fire-Resistance Rating Requirements for Building Elements, the proposed type of construction for Ewing/Cross is type IIIB; fully sprinkled – Unprotected Combustible. The occupancy for the building includes three classifications as defined in chapter 3 of the International Building Code: mixed use residential R-2, assembly A-3, and storage S-1 separated.
The following National Codes were utilized for design:
+ Building Code: 2009 International Building Code
+ Structural Code: 2009 Pennsylvania Uniform Construction Code; 2009 International Building Code; 2009 International Existing Building Code
+ Plumbing Code: 2009 International Plumbing Code
+ Mechanical Code: 2009 International Mechanical Code
+ Electrical Code: 2008 National Electrical Code
+ Fire/Life Safety Code: 2009 International Building Code
+ Fire Protection: NFPA 13
+ Accessibility Code: 2009 International Existing Building Code
Zoning
The South Halls Renovation falls under The Pennsylvania State University’s “University Planned District” which was designed to promote the careful planning and orderly development of the University campus, consistent with the community development goals of the Centre Region and its member municipalities.
+ Maximum Height: 90 feet
+ Maximum Floor Area Ratio: 1.0
+ Maximum Impervious Surface Coverage: 55%
+ Minimum Open Space: Not Less than 45%
Historical Requirements
There are no historical requirements for this building.
Part II
___________________________________________________
Primary Engineering Systems
Construction
Ewing/Cross is under an aggressive 7 month construction schedule, which will hit substantial completion on December 31st, 2013; allowing students to move into the building during the Spring 2014 semester. The project is implements a Design-Build delivery method, with Clark Nexsen as the Architect/Engineer and Barton Malow Construction Company as Construction Manager teaming up. Design-Assist specialty contractors (Mason, Mechanical, Electrical, Plumbing, Fire Protection, Exterior/Interior, and Glass/Glazing) were brought onto the project early during the design phase based on a best value selection.
Structural
Ewing Cross was constructed in 1955 using mainly HSS steel members and Lift Slab Construction. Floors 1-4 consist of 7.5” thick Lift Concrete Structural Slab with HSS Steel Columns, ranging in size from HSS4 1/2x4 1/2 to HSS7x4, as well as W8x28 wide flange members, with the existing roof consists of mainly W8x13 wide flange members. The upper floors are supported at the ground floor by cast-in-place concrete beams that tie into cast-in-place concrete columns, ranging in size from 12”x12” to 16”x27”. These columns distribute the building loads to a 24” thick foundation slab. It was determined that the alternations to the building increased the weight, and therefore the lateral load of the existing building structure by less than 5 percent. Therefore, additional lateral force resistance to the existing building was not required. A majority of the existing structure will remain; will the exception of the bathroom floor slabs.
The renovation of Ewing/Cross includes the addition of a wraparound porch on the south side of the building, twelve (12) stone panel system bump outs on the building’s façade which connect into the roof structure with gabled ends. Spread footings support concrete columns, ranging in size from 1’-0”x1’-0” to 1’-2”x1’-2”, which support the new wrap around porch that ties into the existing porch on the south side of the building with a 6” cast-in-place concrete slab with #4 rebar, which transitions to an 8” cast-in-place concrete slab with #5 rebar. The four (4) stone panel bump outs which house mechanical duct chases are supported by a 6” metal stud wall which ties into a 13” concrete wall supported by a 4’-0” x 2’-0” wall footing, which ties into the existing structure. The other eight (8) projections are supported by 6” metal stud framing, which is secured to the existing brick façade.
The concrete slab-on-grade is 6” thick reinforced with 6x6 wwf. The bathroom floor construction (1-4) consists of a 3 ¼” LW Concrete on 3” deep composite steel deck, reinforced with 6x6 wwf. The composite slab-on-deck was designed as shored composite construction. The new roof gables are constructed from cold-formed steel trusses at 2’-0” OC, on top of cold formed steel channels at 2’-0” OC.
Electrical
Similar to the other buildings at South Halls, Ewing/Cross has a normal feeder and an emergency feeder from Redifer Hall. The system requires a demand service of 354.6 kVA. It is supplied via 480V utility feed that travels through a 600 amp main distribution panel (MDP). From the MDP, service is provided to the major mechanical equipment that requires 480Y/277 (ERV, CHWP, HWP, DTP, CHWP) are supplied. The MDP also supplies the 600 amp existing distribution panel (LDP), via a 150 kVA step-down transformer. The elevators and all of the smaller panel boards are directly supplied via the LDP panel and are rated at 208Y/120 and primarily service the power and lighting loads.
Ewing/Cross implements an emergency power system, which is fed from Redifer Hall. Emergency Power is supplied to an Emergency 3-phase medium voltage switch that feeds into a 75kVA emergency transformer. The transformer services an emergency distribution panel (EDP) which ties directly into the LDP via 208V utility feed, and can used to energize the necessary loads during a power outage.
Lighting
The lighting plan for Ewing/Cross consists of various sizes of T8 fluorescent troffer luminaires, recessed downlight and wall washers led fixtures, and several different compact fluorescent ceiling and wall mounted fixtures. The Common Lounges and Meeting Rooms utilize 2x4 Direct/Indirect fluorescent F28T8 luminaires with three (3) lamps on a dimming ballast. A typical student room makes use of a 1x4 surface mounted fluorescent two (2) lamp F28T8 dimmable fixture with integral occupancy sensor. The sorority suites lighting consists of several 4” diameter led downlight fixtures, along with 24” diameter decorative flush ceiling mounted fluorescent FT36/2G11 fixtures. The typical lamp throughout the building is a F28T8.
Mechanical
Hot and chilled water is supplied from Redifer Hall and is transferred to Ewing/Cross’s system through heat exchangers on the ground floor. There are three (3) main mechanical systems that serve Ewing Cross. The first system is a dual temperature system which provides heating and cooling through 160 individual Fan Coil Units (FCU), which service student bedrooms, sorority suites and lobbies. The FCUs are on a dual pipe system, with a 1” copper supply and a 1” copper return. The second system consists of Two (2) Air-to-Air Energy Recovery Ventilation (ERV) units which are used to supplement the Outside Air by recovering heating/cooling from Exhaust Air; ERV-3 supplies 3,830 CFM to Ewing and ERV-4 supplies 4,370 CFM to Cross. Duct chases from the ERV units at ground floor are ran through the four (4) stone panel bump outs located in front of the bathroom stacks. From these chases, the ductwork branches out to each floor to distribute fresh to each room that runs on a two pipe system. The third system is a Four Pipe System which services the Ground and First Floors Common Areas, such as the lounge, loggia, entrance, and sorority storage. The four pipe system allows for greater flexibility in temperature control by allowing heating and cooling simultaneously. The fan coil units on the four pipe system are tied directly into the ductwork for the space which they service, eliminating runs of ductwork from the ERV to each respective room.
In addition to the three main mechanical systems, special accommodations were made to provide heating and cooling to the two (2) meetings rooms on the first floor; both are fed by separate 1700 CFM Air Handling Units (AHU). This was due to the lack of room for running additional ductwork to the meeting rooms, from the mechanical room on ground floor; the reduced runs of ductwork also provide cost savings.
Fire Protection
The building makes use of a wet pipe sprinkler system for all areas except for the attic, which will remain on the existing dry pipe sprinkler system. All areas are considered light hazard occupancies per NFPA 13, except the basement, mechanical and storage areas, which are considered ordinary hazard group 1 occupancies. All other building elements have fire-resistive ratings in accordance with IBC 2009 Table 601.
Transportation
There are two (2) traction elevators that service the building; one (1) for Ewing and one (1) for Cross, as required by code for handicap access to the upper floors of the building. In addition to the elevators, there is also a wheelchair lift located in stairwell #1, due to 4’-9 5/8” floor height difference between Ewing and Cross.
Telecommunications
Ewing/Cross has the typical telecommunication systems: voice, data and catv cabling is ran to each room. Service Entrance Cabling is run from Redifer Hall through the Utility Tunnel to terminals located on the ground floor. From the ground floor terminals, cabling is distributed to each floor and then to the telecommunications device outlets. Ewing/Cross is also equipped with whole building Wi-Fi.
|